An Analysis of Three Major Detection Standards
Titanium anodes are the backbone of many critical industries, including electrolysis, electroplating, and wastewater treatment. The secret to their performance lies in their specialized surface coatings, which enhance electrocatalytic activity and durability. But how long do these coatings last? And how can you accurately assess their lifespan?
In this guide, we dive deep into three major detection standards used to evaluate titanium anode coatings: Accelerated Life Testing (ALT), Cumulative Charge Quantity and Standard Accelerated Lifetime, and Real-World Operating Condition Simulation Testing. We’ll break down each method, explain how they work, and explore real-world case studies that highlight their importance. Whether you are a manufacturer looking to optimize your product or an industry professional seeking reliable anode solutions, this comprehensive analysis will help you make informed decisions.
I. The Importance of Titanium Anode Coating Lifespan
1. Role of Titanium Anode Coatings
Titanium anode coatings are engineered to:
✔ Enhance electrocatalytic activity – improving efficiency in industrial electrochemical reactions.
✔ Reduce overpotential – lowering energy consumption in processes like chlorine and oxygen evolution.
✔ Increase stability and longevity – ensuring consistent performance over extended periods.
Without a durable coating, titanium anodes degrade quickly, leading to increased costs and operational inefficiencies. That’s why evaluating their lifespan is crucial.
2. Why Lifespan Evaluation Matters
Understanding and optimizing coating lifespan offers several benefits:
- Cost Efficiency: Frequent anode replacement increases production costs. Longer-lasting coatings reduce maintenance expenses.
- Performance Optimization: By analyzing lifespan data, manufacturers can refine coating formulas for enhanced durability and efficiency.
- Market Expansion: Reliable lifespan metrics make titanium anodes more attractive for various industries, including green energy, environmental protection, and large-scale chemical production.
Investing in high-quality, long-lasting titanium anodes is not just a cost-saving measure—it’s a way to enhance productivity and stay ahead of the competition.
II. Accelerated Life Testing (ALT) Method
1. What is Accelerated Life Testing?
Accelerated Life Testing (ALT) is a widely used method to predict anode lifespan by simulating extreme operating conditions. This speeds up the degradation process, providing insights into how long a coating will last under real-world conditions.
2. ALT Testing Conditions
- Electrolyte: Typically 1 mol/L sulfuric acid (H₂SO₄) for its high conductivity and corrosive nature.
- Current Density: 1–6 A/cm² (higher densities accelerate wear and tear).
- Temperature: 40–60°C (higher temperatures simulate prolonged exposure).
3. How to Interpret ALT Data?
Example: A ruthenium-iridium-titanium (Ru-Ir-Ti) coating lasts 2,928.5 hours in 1 mol/L H₂SO₄ at 40°C and 4 A/cm².
💡 What does this mean?
- If an anode survives 4,000 minutes in ALT, it can last 8+ years in a real chlor-alkali production environment.
- Manufacturers use these insights to compare coatings, refine materials, and predict maintenance schedules.
Keawayy Take
ALT is fast and effective, but it may overestimate degradation. That’s why it’s often combined with other testing methods.
III. Cumulative Charge Quantity and Standard Accelerated Lifetime
1. What is Cumulative Charge Quantity?
This metric quantifies the total charge passed through the coating before failure, measured in kA·h/m². It reflects:
✔ Catalytic activity – how well the coating performs over time.
✔ Durability – how resistant the coating is to wear and tear.
2. What is Standard Accelerated Lifetime?
Standard Accelerated Lifetime (SAL) normalizes cumulative charge by iridium (Ir) content, making it easier to compare coatings with different formulations.
Formula:
Standard Accelerated Lifetime = 10⁴ A·h/g(Ir)
3. Real-World Cases
- Case 1: An Ir-Ta coating achieves 11.7×10⁴ A·h/cm² under ALT, with a standard accelerated lifetime of 327.87×10⁴ A·h/g(Ir).
- Case 2: A low-iridium coating achieves 23×10⁴ A·h/g(Ir)—offering cost savings without sacrificing performance.
💡 Key Insight: This method is excellent for comparing coatings and choosing cost-effective yet durable options.
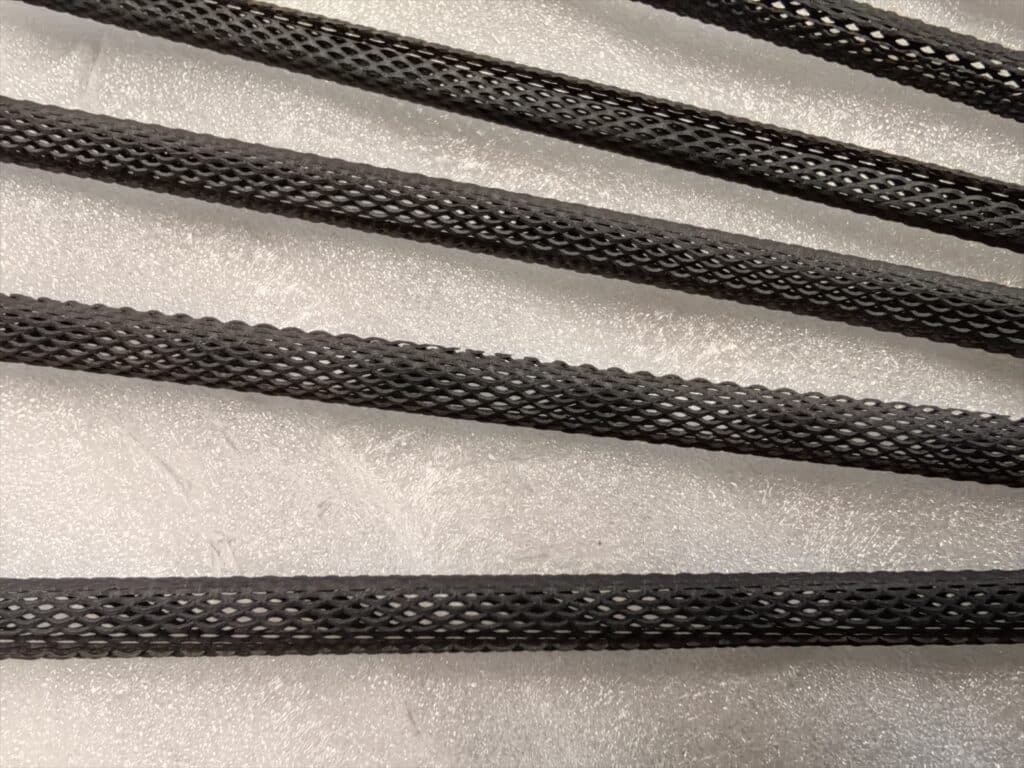
IV. Real-World Operating Condition Simulation Testing
1. What is Simulation Testing?
Real-world operating condition simulation testing is a method used to evaluate titanium anode coatings by replicating actual industrial environments. Unlike accelerated life testing (ALT), which subjects coatings to extreme conditions to speed up degradation, simulation testing aims to assess performance under realistic operating parameters. This approach provides the most accurate representation of how a coating will behave over its expected lifespan, making it a crucial step in validating anode durability before large-scale industrial deployment.
By recreating specific electrochemical environments, this testing method helps manufacturers and researchers determine how coatings respond to real working conditions, including exposure to process-specific electrolytes, industrial current densities, and temperature fluctuations. The data collected from these tests can be used to predict service life, optimize coating formulations, and ensure long-term operational stability in applications such as chlor-alkali electrolysis, electroplating, and wastewater treatment.
2. Typical Testing Conditions
Simulation testing requires precise control over key operational parameters to accurately mimic industrial applications. The primary factors considered include:
-
Electrolyte Composition: The electrolyte used in testing matches the real process environment in which the anode will operate. For example, in chlor-alkali production, a saturated sodium chloride (NaCl) solution is used to simulate the highly corrosive conditions present in industrial electrolysis cells. In electroplating, the electrolyte would reflect the specific metal ion concentrations found in plating baths.
-
Current Density: The applied current density is set according to industrial standards for the specific application. In chlor-alkali electrolysis, current densities typically range between 15–20 A/dm², whereas in electroplating and electrowinning, the values may vary depending on the metal being deposited and the required efficiency of the process.
-
Temperature and pH Control: Maintaining precise temperature and pH levels is essential for an accurate assessment of coating performance. In many electrochemical processes, temperature fluctuations and pH variations significantly impact the rate of anode degradation. Testing protocols ensure that these conditions reflect real-world scenarios to provide meaningful lifespan predictions.
3. How is Data Used?
The results from simulation testing provide essential insights into the durability and efficiency of titanium anode coatings in real-world applications. The primary uses of this data include:
-
Lifespan Assessment: By continuously monitoring anode performance under industrial conditions, researchers can determine the exact point at which the coating begins to degrade or fail. This helps establish accurate service life estimates, which are essential for maintenance planning and cost optimization.
-
Performance Optimization: The data collected during testing allows manufacturers to fine-tune coating formulations to enhance corrosion resistance, electrocatalytic efficiency, and overall durability. By analyzing failure modes under real conditions, adjustments can be made to improve coating adhesion, layer thickness, and material composition.
-
Industrial Validation: Before a titanium anode coating is approved for large-scale deployment, simulation testing provides concrete evidence of its performance in the intended application. This is particularly important for industries that require strict reliability, such as chlorine production, metal refining, and wastewater treatment.
Example Case Study
A ruthenium-titanium (Ru-Ti) coating underwent simulation testing in a saturated sodium chloride (NaCl) solution, replicating the conditions of an industrial chlor-alkali electrolysis cell. The results indicated that the coating remained stable and functional for a period of five years before reaching the end of its operational lifespan. This validated its reliability for long-term use in chlorine production, confirming its suitability for large-scale industrial applications.
By relying on real-world operating condition simulation testing, manufacturers can confidently develop and deploy titanium anode coatings with proven durability, ensuring cost-effectiveness and operational efficiency for industrial users.
V. Comparing the Three Detection Standards: Which One is Right for You?
When evaluating the lifespan of titanium anode coatings, selecting the right testing method is crucial. Each detection standard has its strengths and limitations, making it essential to choose the one that aligns with your specific needs. The table below provides a quick comparison:
Comparison of Three Major Detection Standards
Method | Advantages | Disadvantages |
---|---|---|
Accelerated Life Testing (ALT) | ✅ Fast and efficient lifespan predictions ✅ Allows for rapid comparisons of different coatings ✅ Helps manufacturers quickly refine formulations |
❌ Overestimates wear due to extreme test conditions ❌ Results may not perfectly reflect real-world performance |
Cumulative Charge Quantity & Standard Accelerated Lifetime | ✅ Provides a standardized metric for comparing different coatings ✅ Helps optimize cost-performance balance ✅ Enables manufacturers to reduce precious metal usage while maintaining durability |
❌ Requires precise measurement of iridium (Ir) content ❌ Variability in coating composition may affect comparability |
Real-World Operating Condition Simulation Testing | ✅ Most accurate predictor of real-world anode performance ✅ Helps fine-tune coatings for specific industrial applications ✅ Essential for final validation before large-scale deployment |
❌ Time-consuming and expensive ❌ Requires access to real-world industrial conditions |
Which Testing Method Should You Choose?
Since each method serves a different purpose, the best choice depends on whether the goal is research and development or industrial deployment.
For Research and Development (R&D)
In the early stages of developing or optimizing coatings, a combination of Accelerated Life Testing (ALT) and Cumulative Charge Quantity analysis is recommended.
Why?
- ALT provides quick lifespan predictions, allowing manufacturers to test multiple formulations efficiently.
- Cumulative Charge Quantity enables direct comparison of coatings, ensuring the most cost-effective yet durable option is selected.
Example:
A company developing a low-iridium titanium anode used ALT to screen potential coatings. Cumulative Charge Quantity analysis confirmed that a 40% reduction in iridium content still maintained a seven-year lifespan, leading to significant cost savings.
For Industrial Applications and Large-Scale Deployment
Once a coating has been refined and optimized, it must be validated in real-world conditions before large-scale production. Real-World Operating Condition Simulation Testing is the most reliable method for this stage.
Why?
- It provides accurate data on actual performance under industrial conditions.
- It helps manufacturers fine-tune coatings for specific applications, such as chlor-alkali electrolysis, electroplating, or wastewater treatment.
- It ensures long-term reliability, preventing unexpected failures and costly downtime.
Example:
A wastewater treatment facility tested a Ru-Ti anode using real-world simulation testing. The results confirmed a 10-year lifespan in landfill leachate treatment, securing project approval and reducing long-term replacement costs.
Best Practice: A Combined Approach
For optimal results, many manufacturers use multiple testing methods at different stages:
- ALT for quick screening and preliminary lifespan predictions.
- Cumulative Charge Quantity to compare coatings and ensure cost-efficiency.
- Real-World Simulation Testing before large-scale deployment to confirm long-term performance.
Using all three methods strategically helps balance speed, cost-effectiveness, and accuracy, ensuring titanium anodes deliver maximum efficiency and durability in industrial applications.
If fast results are needed, ALT is the best choice. If a standardized comparison is required, Cumulative Charge Quantity is useful. If real-world validation is necessary, Simulation Testing provides the most reliable data. Combining all three methods at different stages ensures the best overall outcome.
VI. Case Studies: Real-World Success Stories
Titanium anode coatings play a critical role in industries that rely on electrochemical processes. The lifespan and performance of these coatings directly impact operational costs, efficiency, and long-term sustainability. The following case studies highlight how different evaluation methods—Accelerated Life Testing (ALT), Cumulative Charge Analysis, and Real-World Operating Condition Simulation Testing—have been successfully used to optimize titanium anode coatings for various industrial applications.
1. Chlor-Alkali Industry: Extending Anode Lifespan and Reducing Costs
Background
The chlor-alkali industry is one of the largest consumers of titanium anodes. These anodes are used in electrolysis cells to produce chlorine gas and sodium hydroxide from brine (sodium chloride solution). Given the harsh operating conditions—high current densities, highly corrosive electrolytes, and elevated temperatures—anode coatings must be durable and stable over long periods.
Challenge
A leading chlor-alkali production facility was facing frequent anode replacements due to premature coating degradation. The company sought a solution that would extend anode lifespan while reducing maintenance and replacement costs.
Solution
Using Accelerated Life Testing (ALT), researchers evaluated a ruthenium-iridium-titanium (Ru-Ir-Ti) coating under extreme conditions to predict its long-term durability. The ALT results estimated that the new coating could last up to eight years in actual production conditions.
Results
After implementing the new Ru-Ir-Ti anodes, the facility confirmed that the anodes maintained stable performance over the predicted eight-year period. This significantly reduced anode replacement frequency, cutting operational costs by 18%. The extended lifespan also led to fewer production interruptions, improving overall process efficiency.
Key Takeaway
By using ALT as a predictive tool, the chlor-alkali industry was able to develop and implement a long-lasting titanium anode coating, leading to cost savings and enhanced production reliability.
2. Electroplating Optimization: Reducing Precious Metal Usage Without Sacrificing Performance
Background
The electroplating industry uses titanium anodes to deposit metal coatings onto various substrates. Precious metals such as iridium and ruthenium are commonly used in anode coatings to enhance durability and performance. However, these materials are expensive, and reducing their usage without compromising performance is a key goal for cost efficiency.
Challenge
An electroplating company was searching for a way to reduce the iridium content in its anode coatings while ensuring that the anodes maintained their required lifespan and electrochemical efficiency.
Solution
Researchers conducted Cumulative Charge Quantity analysis to compare different coating formulations. The goal was to identify a lower-iridium composition that could achieve the same level of durability as higher-iridium coatings. Through this method, a new coating with 40% less iridium was identified while still maintaining strong catalytic activity.
Results
The newly developed low-iridium coating was tested in production and demonstrated a seven-year lifespan, which was comparable to the high-iridium coating previously used. The 40% reduction in iridium usage led to significant cost savings while ensuring that electroplating efficiency remained unchanged.
Key Takeaway
By leveraging Cumulative Charge Quantity analysis, the company successfully developed a cost-effective anode coating that reduced reliance on precious metals while maintaining high performance and durability.
3. Wastewater Treatment: Validating Anode Durability in Harsh Environmental Conditions
Background
Titanium anodes are increasingly used in wastewater treatment to degrade organic pollutants and remove heavy metals through electrochemical oxidation processes. However, wastewater treatment environments are highly variable, with fluctuating pH levels, chemical compositions, and contaminants that can accelerate anode degradation.
Challenge
A municipal wastewater treatment facility needed to install titanium anodes for the electrochemical treatment of landfill leachate, one of the most challenging wastewater types. The anodes had to withstand extreme chemical conditions while maintaining a long operational lifespan.
Solution
Before large-scale deployment, Real-World Operating Condition Simulation Testing was conducted to evaluate the durability of titanium anodes with a ruthenium-titanium (Ru-Ti) coating under actual landfill leachate conditions. Testing parameters included exposure to:
- High concentrations of organic pollutants
- Fluctuating pH levels ranging from highly acidic to neutral
- Chloride-rich environments that accelerate corrosion
Results
Simulation testing confirmed that the Ru-Ti coated anodes maintained stable performance for ten years without significant degradation. This validation provided the necessary technical assurance for project approval, allowing the wastewater treatment facility to proceed with installation.
Key Takeaway
By using simulation testing, the facility avoided premature failures and unexpected costs, ensuring that the anodes provided long-term reliability in a highly aggressive wastewater environment.
VII. Future Trends in Titanium Anode Coatings
🚀 Coating Innovations
✔ Low-PGM Coatings: Reducing reliance on iridium/ruthenium to lower costs.
✔ Non-PGM Coatings: Exploring iron, nickel, or carbon-based alternatives.
🔬 Advanced Testing Technologies
✔ AI-Powered Testing: Automating failure predictions for higher accuracy.
✔ Digital Twins: Simulating anode degradation using real-time data.
🌍 Sustainability and Standardization
✔ ISO/IEC Standards: Global efforts to unify testing protocols.
✔ Carbon Footprint Metrics: Integrating environmental impact into lifespan analysis.
Selecting the right titanium anode is not just a technical decision—it is a strategic investment that impacts operational efficiency, cost management, and long-term sustainability. High-quality titanium anodes with advanced coatings ensure longer service life, reduced maintenance costs, and improved electrochemical performance in industries such as chlor-alkali production, electroplating, and wastewater treatment. Inferior anodes degrade faster, leading to frequent replacements, increased downtime, and higher operational costs. Investing in a premium titanium anode with a scientifically optimized coating means fewer replacements and lower overall expenditure. For example, anodes developed using Accelerated Life Testing (ALT) and Real-World Simulation Testing can last up to 10 years in harsh industrial environments, significantly reducing replacement frequency. The effectiveness of an anode directly impacts energy consumption and product quality. Precision-engineered coatings, such as Ru-Ir-Ti or low-PGM alternatives, reduce overpotential, improve electrolysis efficiency, and provide superior corrosion resistance. This results in lower energy consumption and optimized electrochemical reactions, making your industrial processes more sustainable and cost-effective. Industrial processes involve extreme conditions—high current densities, aggressive electrolytes, fluctuating pH levels, and elevated temperatures. High-quality titanium anodes are designed to withstand these challenges, ensuring consistent performance and long-term stability. At Ehisen, all anodes undergo rigorous testing, including ALT, cumulative charge analysis, and real-world condition simulation, to guarantee durability in the most demanding environments. Not all titanium anodes are created equal. At Ehisen, our anodes are scientifically tested and validated using industry-leading methods to ensure longevity and efficiency. Through case studies in the chlor-alkali industry, electroplating sector, and wastewater treatment facilities, our anodes have demonstrated up to 40% cost savings in precious metal usage and significant improvements in lifespan. Sustainability is a growing concern across industries. Ehisen’s titanium anodes are designed with low-PGM (precious group metal) and non-PGM coating alternatives that minimize resource consumption while maintaining high performance. This not only reduces operational costs but also supports global sustainability initiatives. At Ehisen, we specialize in designing and manufacturing high-quality, long-lasting titanium anodes tailored to your specific industrial applications. Our products are backed by: If you’re looking for scientifically tested, long-lasting titanium anodes that provide cost savings, operational efficiency, and superior durability, Ehisen is your trusted partner. 📞 Get in touch with us today to discuss your specific requirements and find the best titanium anode solutions for your industry. Visit Ehisen’s website or contact our technical team for expert guidance. Let us help you enhance efficiency, reduce costs, and maximize the lifespan of your titanium anodes.Conclusion: Why Choose High-Quality Titanium Anodes?
1. Long-Term Cost Savings
2. Enhanced Performance and Efficiency
3. Reliability in Challenging Conditions
4. Proven Scientific Validation
5. Sustainable and Environmentally Friendly Solutions
Why Choose Ehisen for Your Titanium Anode Needs?
✅ Advanced Coating Technology: Optimized for efficiency and longevity.
✅ Proven Testing and Validation: Scientifically assessed using industry-leading methods.
✅ Custom Solutions: Tailored to meet your process requirements and environmental conditions.
✅ Reliable Supply and Technical Support: Ensuring seamless operation and expert guidance.Contact Ehisen Today for Reliable Titanium Anodes
4 Responses
Hɑѵing read this I believed it was extremely informative.
I appreciate you finding the time and energy to put this short
article together. I once again find myself spending a significant
amount of timе botһ reading and pоsting comments. But so what,
it ᴡas still worth it!
Thank you for your reply. As a professional titanium anode manufacturer, we will share more relevant knowledge.
I congratulate, what words…, a brilliant idea
Thank you for your reply. As a professional titanium anode manufacturer, we will share more relevant knowledge.