Precision Development for Superior Performance
At Ehisen, we specialize in advanced coating solutions for titanium anodes, using precisely formulated precious metal solutions. With patented coating technology and a strong R&D capability, we continually optimize coating formulas based on customer feedback, helping to significantly reduce procurement costs. Our titanium anodes, including Iridium-Tantalum, Ruthenium-Iridium, Platinum-Coated, and MMO (Mixed Metal Oxide) anodes, offer exceptional durability, catalytic efficiency, and operational stability. These products are widely used in industries such as hydrogen production, electroplating, water treatment, and cathodic protection. We work closely with customers to advance coating technologies, delivering cost-effective and reliable electrochemical solutions.
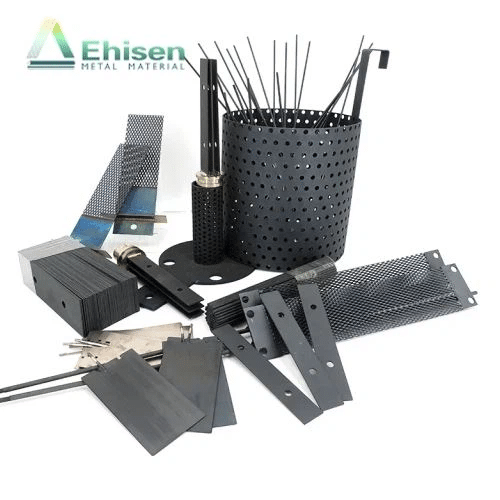
Iridium-Tantalum Titanium Anode
Iridium-Tantalum titanium anodes provide outstanding corrosion resistance and catalytic efficiency, excelling in oxygen evolution reactions (OER). Designed for high current densities and corrosive conditions, they are widely used in hydrogen production, industrial oxidation, and precious metal recovery. Optimized coating formulas extend service life, enhance stability, and reduce operating costs, ensuring consistent performance in demanding environments.
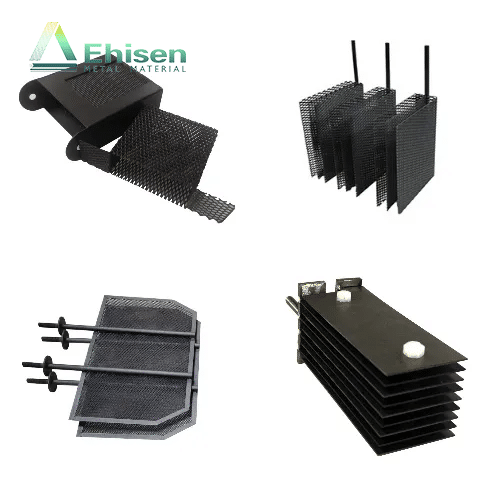
Ruthenium-Iridium Titanium Anode
Ruthenium-Iridium titanium anodes are designed with a balanced coating blend, offering superior performance for chlorine evolution reactions (CER). These anodes are ideal for chlor-alkali production, electroplating, and wastewater treatment. Featuring high corrosion resistance and energy efficiency, they provide long-lasting, reliable service, even in harsh industrial conditions, with tailored formulas that enhance stability and lifespan.
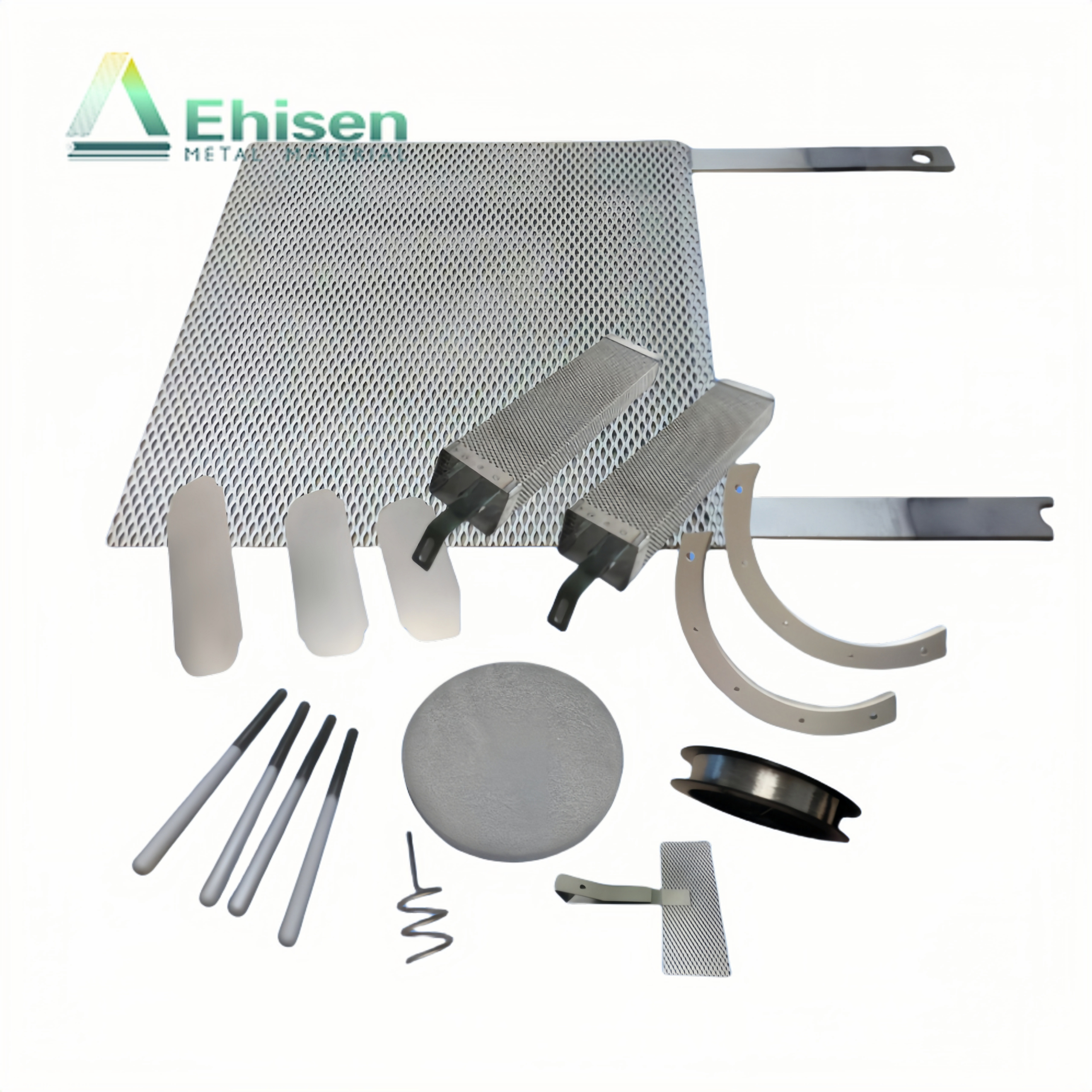
Platinum-Coated Titanium Anode
Platinum-coated titanium anodes are engineered for applications requiring high chemical stability and corrosion resistance. Suitable for oxygen and hydrogen evolution reactions, they are widely used in electronic plating, semiconductor manufacturing, and marine engineering. With precise platinum coatings, these anodes deliver excellent conductivity, long service life, and superior performance for precision-driven industries.
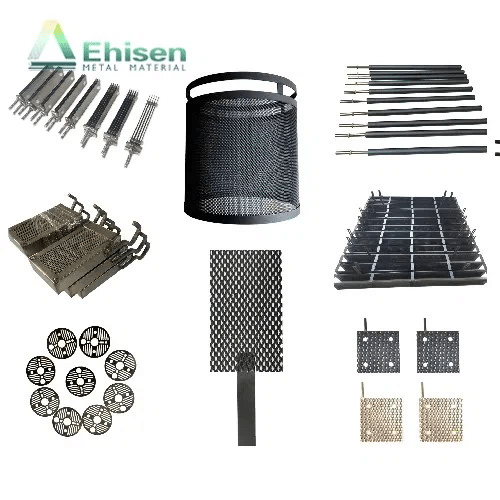
MMO Titanium Anode
MMO (Mixed Metal Oxide) titanium anodes combine multiple metal oxides for exceptional performance in hydrogen evolution reactions (HER) and cathodic protection. Commonly used in corrosion protection systems, chlorine generators, and wastewater treatment, these anodes feature strong adhesion, corrosion resistance, and low maintenance. Optimized coatings improve efficiency and reliability, offering cost-effective solutions for industrial applications.
Precious Metal Coating R&D Laboratory
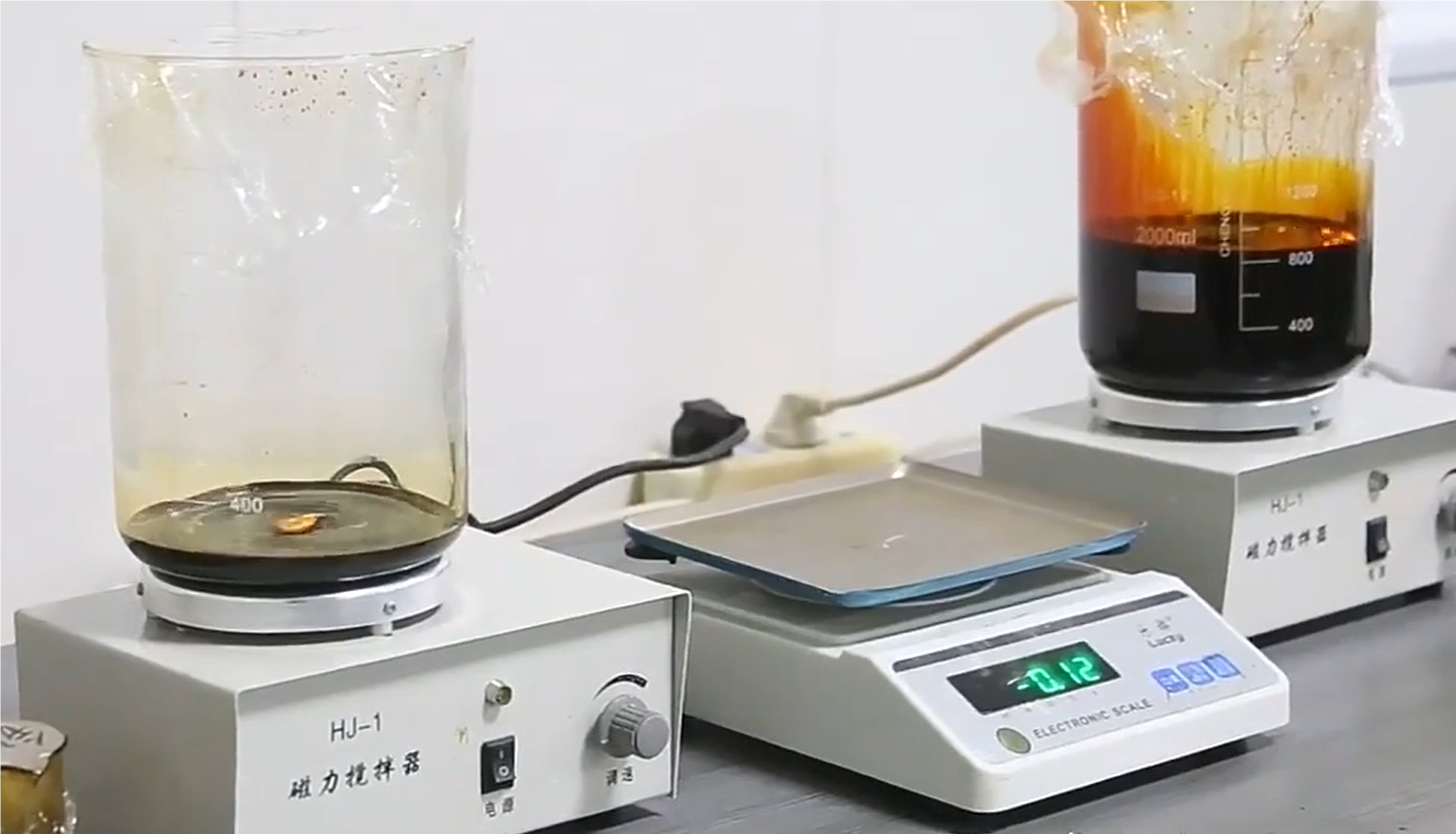
About Us
Why Choose Ehisen for Precious Metal Coating on Titanium Anodes?
At Ehisen, we specialize in optimizing the precious metal coatings of titanium anodes to meet your specific needs. Here’s how we bring value to your projects:
World-Class Expertise in Electrochemical Coatings
Our technical team, led by Ph.D. graduates in electrochemistry from Japan's Tohoku University, possesses cutting-edge research and development capabilities. This ensures that every coating we design meets the highest standards of performance and reliability.
Tailored Coating Ratios for Optimal Results
Collaborating with a diverse range of domestic and international clients, we refine coating ratios and additives to maximize performance. Many customers have already provided positive feedback on how our custom solutions enhanced their operations.
Precision-Driven Design Based on Your Parameters
By analyzing your specific requirements, we calculate the most suitable coating composition and identify the ideal additives to enhance your anode’s functionality. This ensures precision in every solution we deliver.
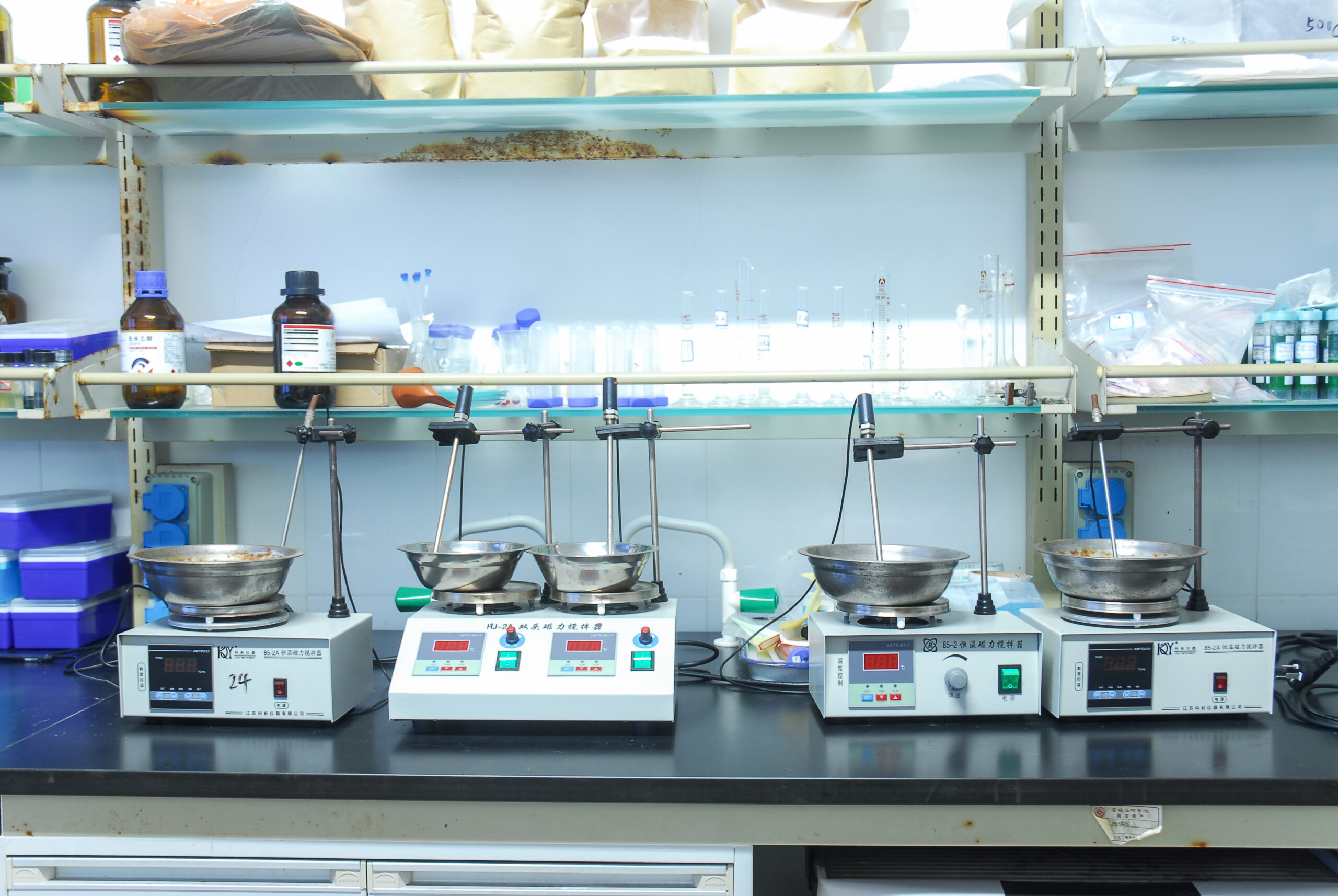
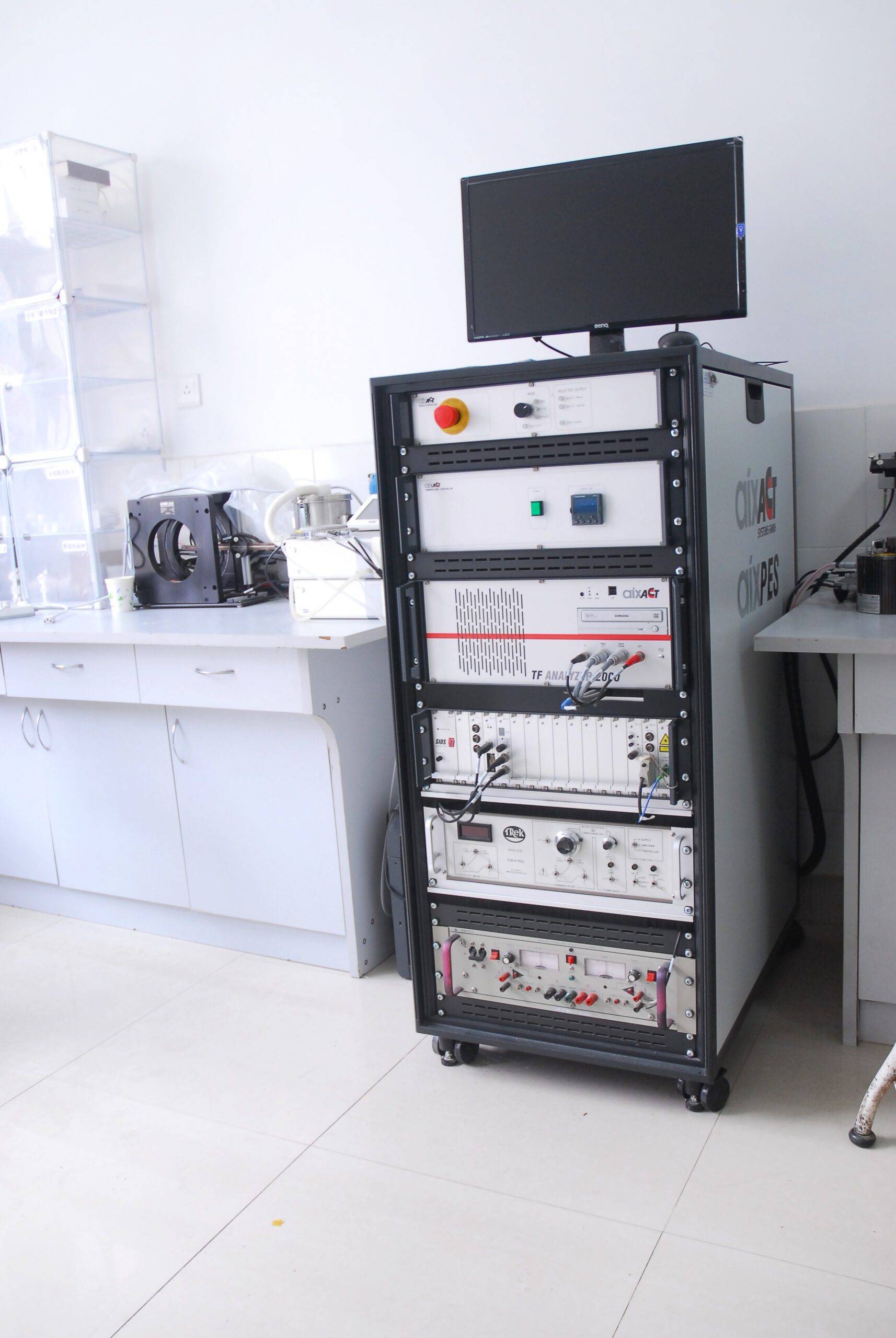
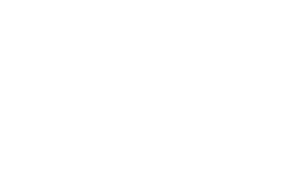
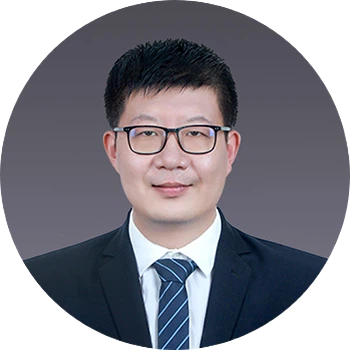
Dr. Miao
Technical Director of Ehisen
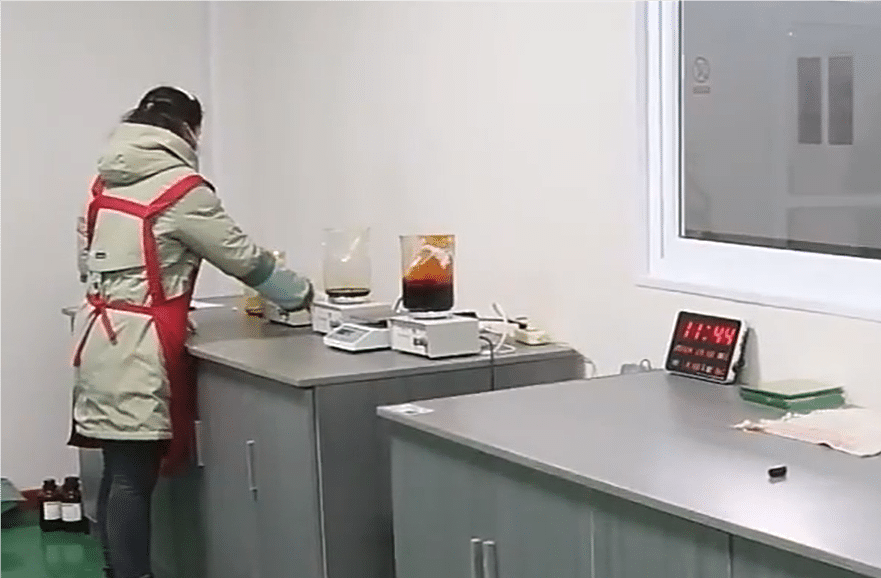
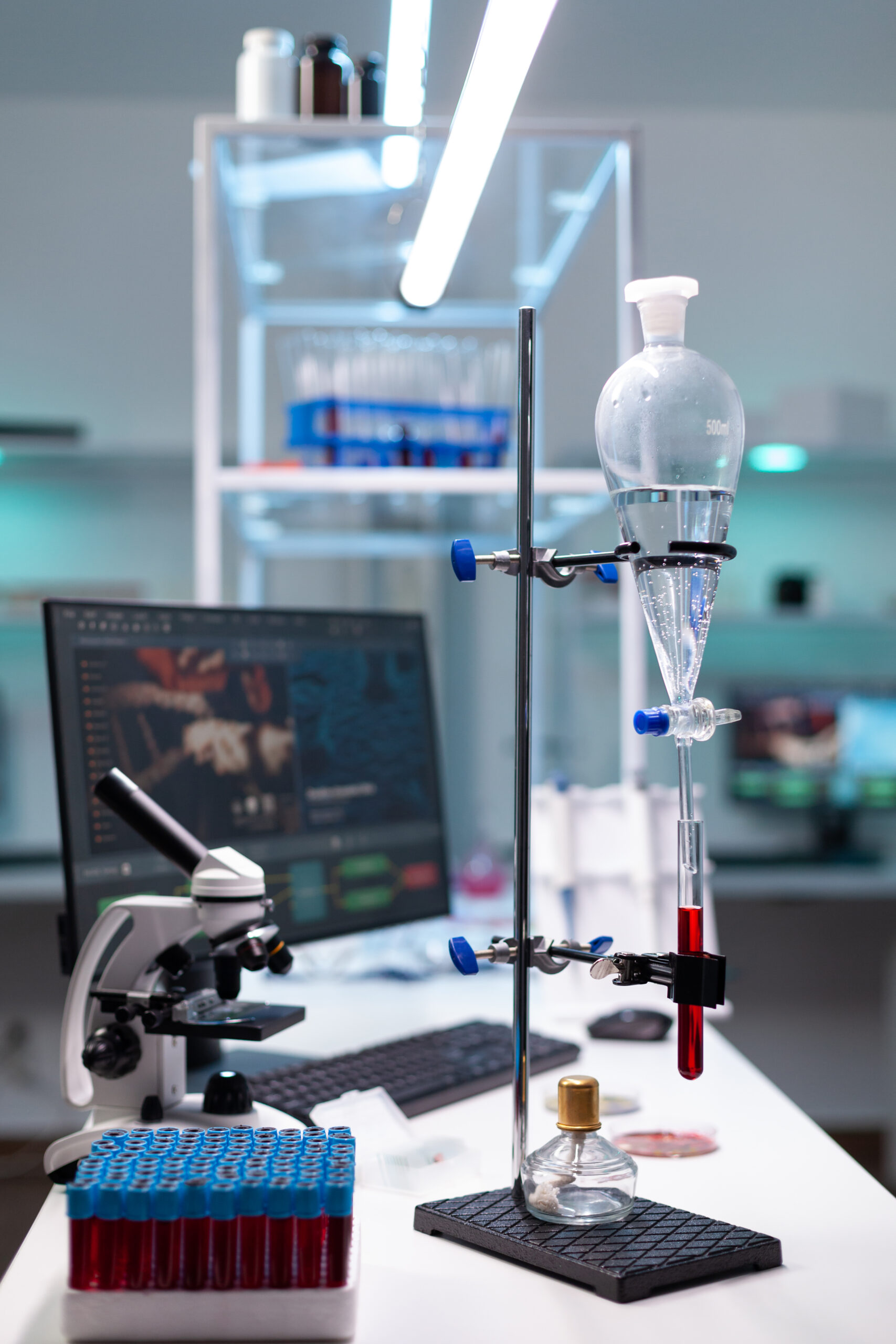
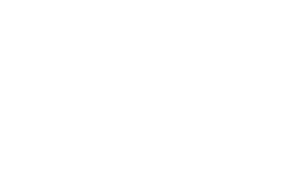
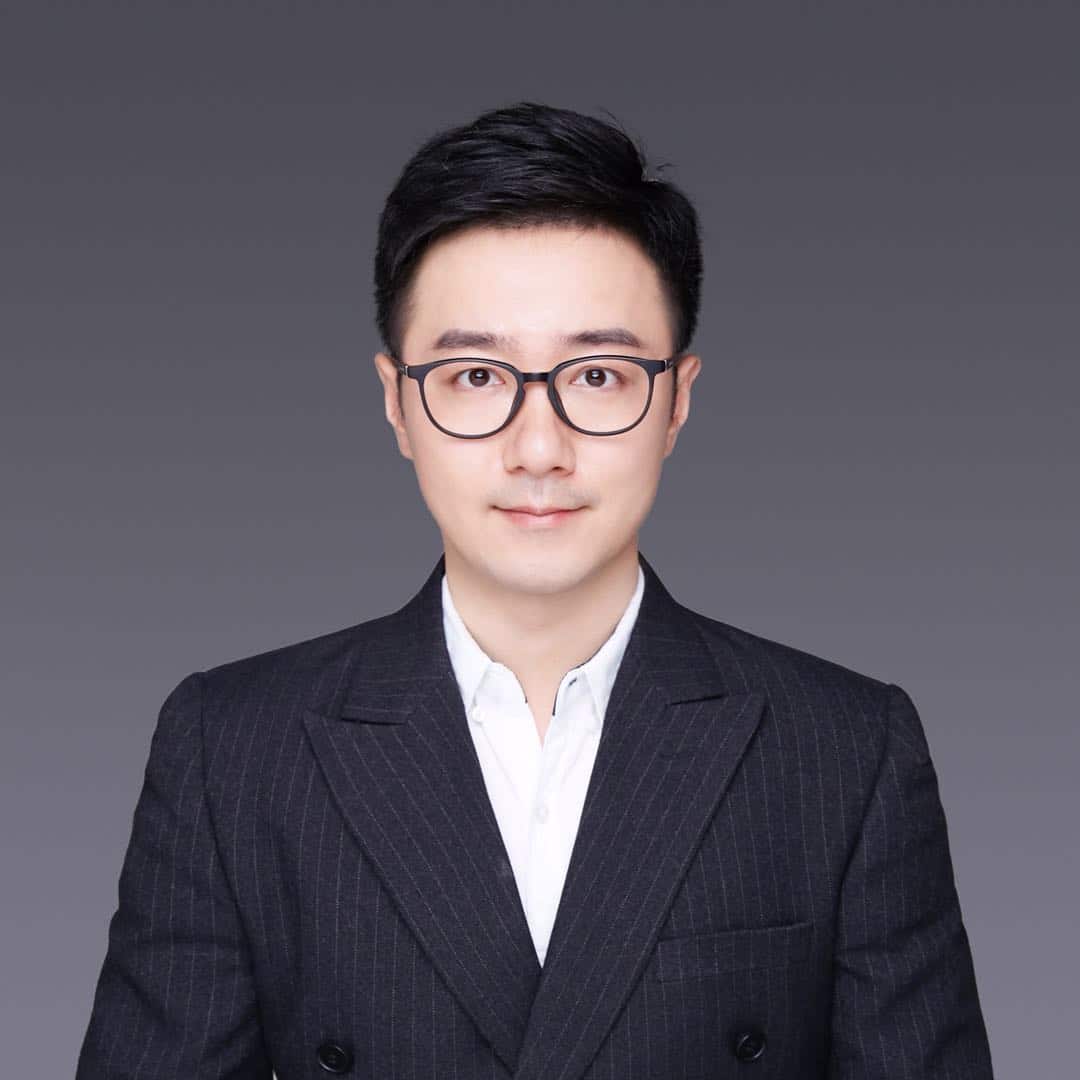
Spencer Xu
CEO of Ehisen
Academic and Industrial Collaboration
Partnering with prestigious Chinese universities, we actively participate in research projects and leverage advanced laboratory equipment to validate and improve our coatings. This synergy allows us to push the boundaries of innovation and deliver state-of-the-art solutions.
Sustainable Recycling Solutions
We offer precious metal recycling services, extracting valuable materials from used titanium anodes. This capability allows us to produce cost-effective coatings for environments with less stringent performance requirements, reducing costs while promoting sustainability.
Industry Engagement and Continuous Improvement
As active participants in titanium industry alliances, we attend regular summits and forums to stay informed of the latest industry trends. This enables us to remain at the forefront of innovation and share valuable insights with our clients.
Why Understanding Precious Metal Coating Ratios Is Essential for Procurement Professionals
For procurement professionals sourcing titanium anodes, grasping the importance of precious metal coating ratios is a game-changer. These ratios determine not only the performance and lifespan of the anodes but also provide transparency in pricing structures. At Ehisen, we offer detailed guidance on coating composition—whether ruthenium-iridium, iridium-tantalum, or platinum—tailored to specific operating conditions and requirements. By understanding how coating precious metal content and ratios align with your application, you can accurately evaluate quotes, ensure compatibility with your usage scenarios, and confidently assess supplier pricing fairness. This insight empowers informed decision-making and avoids costly mismatches in performance expectations.
Table of Contents
Chapter 1:Introduction of titanium anode precious metal solution
Common Precious Metal Coating Types & Their Applications
1. Why Understand Titanium Anode Precious Metal Coatings?
In practical use, different precious metal coatings offer varying levels of electrochemical performance, corrosion resistance, and service life. As a buyer, you need to match your industry’s operating environment, performance requirements, and budget to determine which coating best suits your process.
2. Precious Metal Coating Comparison Table
This table summarizes four common types of precious metal coatings—ruthenium-based (Ru), iridium-based (Ir), platinum-based (Pt), and Mixed Metal Oxide (MMO)—along with their key features, typical industries, and approximate price ranges (represented by “$” symbols). Actual costs will depend on coating thickness, precious metal loading, and the supplier’s manufacturing process.
Coating Type | Key Components | Performance Features | Typical Industries | Price Range | Possible Alternatives |
---|---|---|---|---|---|
Ruthenium (Ru-based) | RuO₂, RuCl₃ | – Good catalytic activity for chlorine evolution- Moderate to high corrosion resistance- Stable in acidic/neutral environments | Chlor-Alkali, chlorine productionGeneral water treatment, chlorine electrolysis | $-$$ | – Can be combined with Ir, Pt, or other metals- Limited performance/life if replaced entirely by cheaper metals |
Iridium (Ir-based) | IrO₂, IrCl₃ | – Excellent corrosion resistance, especially in strong acids or highly oxidative conditions- High conductivity and oxidation resistance- Highly efficient for oxygen evolution, electrochemical oxidation | Electroplating, electrochemical oxidationIndustrial wastewater treatment | $-$$ | – Often mixed with Ru or Pt for specific reactions- Replacing it fully can be expensive and requires careful evaluation |
Platinum (Pt-based) | Pt, Pt Black, Pt Salts | – Very high chemical stability, outstanding corrosion resistance and conductivity- Ideal for harsh conditions or high-end chemical/electrochemical processes- More expensive | Pharmaceuticals, fine chemicalsPrecious metal recovery, electroanalysis | $-$$ | – Hard to replace with cheaper metals without losing performance- Thin-layer Pt or alloy approaches may help reduce cost |
Mixed Metal Oxides (MMO) | Ru, Ir, Ti oxides, etc. | – Combines advantages of multiple metals (corrosion resistance, good conductivity)- Formulations can be tailored to specific applications- Offers good stability and overall value | Chlor-Alkali, electroplating, seawater electrolysisWater treatment, general electrochemistry | $-$$ | – Performance may drop if key metal content is reduced- Often used in combination with Ru, Ir, or Pt to optimize performance |
Note:
- “$” is only a rough indicator and does not reflect exact pricing. Precious metal coatings are customized processes, and the price range is based on the customer’s specific conditions of use.
- Actual quotes can vary due to market fluctuations in precious metal costs, coating thickness, and manufacturing methods.
3. Performance & Cost Differences Among These Four Coatings
Ruthenium (Ru-based)
- Strengths: Good for chlorine evolution (like in chlor-alkali plants), less expensive than platinum.
- Typical Uses: Chlor-alkali processes, chlorine-based solutions, water disinfection.
- Cost Control: Less costly compared to platinum; however, its stability is generally lower than iridium. Very mature for chlorine-generating processes.
Iridium (Ir-based)
- Strengths: Outstanding resistance to strong acids and oxidation; durable even under harsh conditions.
- Typical Uses: Electroplating, electrochemical oxidation (ozone generation, organic oxidation), industrial wastewater treatment.
- Cost Control: Iridium supply and pricing can be unpredictable. Though higher-priced, its longer service life in tough environments can reduce overall costs.
Platinum (Pt-based)
- Strengths: Excellent chemical inertness, corrosion resistance, and conductivity; ideal for highly demanding or niche electrochemical applications.
- Typical Uses: Pharmaceuticals, fine chemicals, precious metal recovery, precise electroanalysis.
- Cost Control: Platinum is a rare and costly metal. It’s often only cost-effective where product purity and extreme conditions justify the investment.
Mixed Metal Oxides (MMO)
- Strengths: Flexible formulas can combine various metals (Ru, Ir, Ti, etc.) for a balance of cost and performance; widely used in multiple industries.
- Typical Uses: Chlor-alkali, plating, seawater electrolysis, antifouling, water treatment, general electrochemistry.
- Cost Control: Adjusting metal content can optimize both performance and budget. A popular choice due to its adaptability and cost-effectiveness.
4. Can Non-Precious Metals Replace These Coatings?
Feasibility of Replacement
- For low-demand environments, coatings with reduced precious metal content might suffice, but may shorten service life or reduce efficiency.
- With high current densities or corrosive solutions, cheaper metals typically fall short, leading to higher long-term costs or performance issues.
Doping or Alloying
- Some suppliers add trace metals (e.g., Ta, Pd, Sb) to Ru or Ir to improve specific properties or cut costs.
- Buyers should check test reports (e.g., catalytic activity, lifespan) to ensure the doped coating meets their process requirements.
Composite Coatings
- Layering different coatings or metal oxides (e.g., Pt first, then Ru-Ir) may combine multiple benefits.
- Usually requires custom solutions and upfront testing by specialized manufacturers.
5.From Requirements to Coating Content
5.1. Provide Clear Process Information
- Operating Environment: Specify the electrolyte type (chloride, sulfuric acid, seawater, etc.), operating temperature, and pH range.
- Working Current Density: Estimate or provide typical current densities (e.g., 5 A/dm², 10 A/dm²).
- Operating Time & Lifetime Needs: Will the anode run 8 hours a day or 24/7? Is the planned service life 1 year, 3 years, or longer?
- Industry & Production Scale: Different industries have varying demands for anode lifespan, process stability, and safety. Production volume also affects raw material costs and ROI.
5.2. How Suppliers Convert Your Information into “Precious Metal Usage”
- Matching Electrochemical Parameters: Based on current density and corrosiveness of the solution, suppliers estimate how many grams of precious metals (Ir, Ru, Pt, etc.) or what coating thickness is needed.
- Balancing Lifetime & Cost: For high current density in highly corrosive environments, a higher ratio of precious metals (Ir or Pt) is often required, raising costs but extending anode life.
- Coating Technology: Each supplier’s process differs. The same amount of precious metal can yield different catalytic activity and durability depending on the manufacturing method.
5.3. Why This Matters to Buyers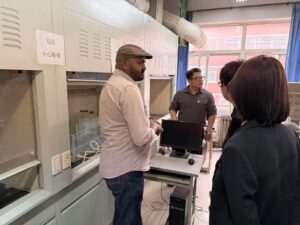
- Evaluating Price Differences: Each supplier’s choice of Ru, Ir, Pt, or MMO coatings—and how many grams of precious metals are used—directly affects the quote.
- Understanding Investment & Return: If the precious metal content is too low, the anode may fail prematurely; too high and initial costs soar. Finding the right balance is key.
- Ensuring Production Stability: In tough environments (e.g., highly oxidative solutions or high temperatures), insufficient precious metal content can lead to higher maintenance and downtime costs than any initial savings.
5.4. Communicating Coating Requirements Effectively
- Share Detailed Process Data: Include specifics like chemical composition, temperature, flow rate, pH, and production targets.
- Compare Multiple Suppliers: Request lab-based accelerated life tests, real-world case studies, or third-party validation.
- Consider Maintenance & Replacement Costs: Think about total cost of ownership (TCO) instead of just the initial purchase price. Factor in anode lifespan and operational efficiency.
5.5. Key Takeaways
- By understanding how precious metal grams and coating formulas vary with different operating conditions, you can better judge supplier quotes and technical proposals.
- A sensible investment in the right coating can reduce downtime, maintenance, and electricity consumption, maximizing the value of your titanium anodes.
Conclusion
By understanding how precious metal coatings work—how many grams are needed, the right coating thickness, and how to balance cost and performance—you’ll be in a much better position to communicate your specific requirements. From our standpoint as a supplier, this clarity greatly streamlines collaboration. The more precisely you can describe your process environment and goals, the easier it is for us to recommend an optimal coating solution.
If you’d like to test your operating conditions first, Ehisen can provide titanium anode samples for trial runs. For a custom product like titanium anodes, the best way to save on cost in the long run is to find the most suitable coating ratio for your needs—one that ensures both efficiency and durability.
Common Precious Metal Coating Ratios & Their Impact on Service Life
1. Typical Market Ratios
The table below shows standard coating systems along with usual ratios or thicknesses. Actual values may vary due to anode shape, operating conditions, and required current density.
Coating System | Typical Ratios / Thickness / Loading | Main Uses & Features | Advantages | Limitations / Notes |
---|---|---|---|---|
Ru-Ir System | – Common ratios: 8:2, 7:3, 6:4 (by mole or weight) – About 5–15 g of metal/m², adjustable to needs | – Used in chlor-alkali, electroplating, wastewater treatment – Good for chlorine evolution, corrosion-resistant, combines Ru’s high activity with Ir’s stability | – More balanced cost & performance than single Ru or Ir – Longer service life vs. pure Ru | – Higher Ir content raises cost – Needs careful assessment under strong oxidation or very high current |
Ir-Ta System | – Ir content often around 5–18 g/m² (adjusted for corrosion/lifespan) – Ratios like 70% Ir : 30% Ta possible | – Common in electrochemical oxidation, ozone generation, strong acid environments – Exceptional corrosion resistance, especially in highly acidic, oxidizing media | – Longer service life – Handles high current densities with good stability | – Ir price fluctuates, so total cost can be high – Insufficient Ta content may reduce corrosion resistance |
Pt-Based System | – Plating thickness usually 0.5–10 μm – Or by weight (e.g., 5–20 g Pt/m²) but must balance substrate vs. coating to ensure good adhesion | – Used in harsh or high-purity settings (pharma, fine chemicals, electroanalysis) – Pt is highly inert, offers excellent corrosion resistance and conductivity | – Superb corrosion resistance and conductivity – Ideal for ultra-pure applications | – Pt is expensive – Excessive thickness can raise costs sharply; poor substrate adhesion lowers performance |
Note: These figures are broad guidelines. Actual ratios and thicknesses depend on factors like electrolyte chemistry, temperature, pH, operating hours, and production needs.
2. The Role of Additives in Precious Metal Coatings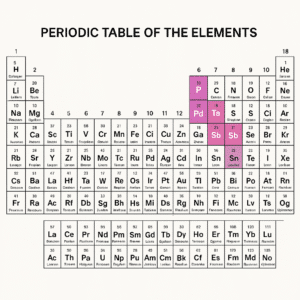
Types of Additives
- Metal Doping: Elements like Pd, Ta, Sb can enhance catalytic activity or corrosion resistance.
- Stabilizers: Help maintain coating integrity in high-temperature or strongly oxidative settings, reducing metal loss.
- Dispersants: Ensure metal particles spread evenly on the surface, improving adhesion and density.
Impact Range
- Service Life: Proper additives can significantly prolong anode life and cut down on repairs.
- Electrochemical Efficiency: Boost the efficiency of specific reactions (e.g., better chloride or oxygen evolution).
- Cost: Usually used in small amounts, but rare or exotic additives can drive up expenses. Evaluate cost vs. performance gain.
Points to Consider
- Side Reactions: Some additives may cause passivation or unwanted by-products under certain conditions.
- Pre-Testing: Lab-scale or accelerated aging tests are advised to ensure additives work as intended in real conditions.
3. Real-World Use: Composite Coatings & Case Study
Principles of Composite Coatings
- Applying multiple layers or mixing various metals (e.g., Pt base for high conductivity + Ir-Ta for corrosion resistance) to achieve superior overall performance.
- Suitable for demanding electrochemical applications with complex operating conditions.
EDI titanium anode[/caption]
Case Study: EDI Titanium Anode with Composite Coating
- Background: A customer sought to increase conductivity by first plating a thin Pt layer on titanium, then adding an Ir-Ta coating.
- Issue: In actual use, chlorine gas produced by the anode ended up damaging the water purification membrane, reducing EDI efficiency.
- Analysis: While conductivity improved, the potential chlorination effect on membranes was overlooked. This highlights that “more metals” doesn’t automatically mean “better”—the entire process, including by-products and compatibility with components like membranes, must be evaluated.
Practical Tips
- Thorough lab simulation or pilot testing is crucial before deciding on composite coatings to avoid unexpected field issues.
- For membrane-based or high-purity processes, always check for chemical or physical damage from by-products like chlorine.
4. Key Steps to Choosing the Best Coating Ratio
- Clarify Operating Conditions & Goals: Know your electrolyte type, temperature, pH, current density, and required anode lifespan.
- Balance Cost vs. Maintenance: Consider upfront investment vs. how often the anode might need servicing, and potential downtime costs.
- Collaborate with Experienced Suppliers: They usually have proven test data and real-world examples to guide you to the right metal loading.
- Pilot Testing & Accelerated Aging: Validate coating performance in lab or small-scale runs to confirm it meets your requirements.
- Stay Flexible: As metal prices or production demands change, you may need to adapt the coating formula to maintain the best cost-performance ratio.
Summary
Different coating systems—Ru-Ir, Ir-Ta, Pt-based, or composites—excel in different scenarios. The real-life lifespan of a titanium anode depends not only on precious metal loading or thickness but also on how well the coating suits your actual working environment. By thoroughly communicating with a knowledgeable supplier, running small-scale tests, and reviewing performance data, you can select the ideal coating formula that strikes a balance between optimal performance and overall cost-effectiveness.
Precious Metal Ratios, Cost Control & Economic Benefits
1. Precious Metal Costs: A Major Factor in Titanium Anode Pricing
High Cost of Precious Metals
- Metals like iridium, platinum, and ruthenium have global market prices that fluctuate based on supply, demand, and other factors.
- These metals often represent the largest share of a titanium anode’s cost, directly impacting the final price.
Ratios Determine Material Usage
- Different mixtures (e.g., Ir-Ta, Ru-Ir, Pt thickness, etc.) dictate how many grams of metal are needed per square meter or per anode.
- Higher metal loading raises costs; too little risks shorter service life or reduced performance.
Value Chain Transparency
- When clients provide demanding parameters (e.g., high current density, harsh chemicals, long lifetime requirements), more precious metals are typically needed.
- With a consistent manufacturing process, the amount (in grams) of precious metal used can be clearly calculated, giving buyers a direct way to assess cost.
Reference Note: According to industry journals (e.g., Electrochemical and Solid-State Letters), prices for Ru, Ir, and Pt have varied widely over the last decade. Both suppliers and buyers should keep an eye on market trends to plan more flexible quotes and purchases.
2. Balancing Performance & Economics: Choosing the Right Metal Concentration
The Risk of Over-Concentrating
- Simply adding more precious metal dramatically increases the initial purchase cost. If your process doesn’t truly need such high-grade durability or efficiency, it could be wasted money.
- For instance, adding too much iridium to an Ir-Ta system may not yield a proportional increase in lifespan, so practical checks are essential.
The Hidden Costs of Under-Concentrating
- Trying to cut costs by drastically lowering metal loading can shorten the anode’s lifespan, requiring frequent replacements or downtime.
- Lower electrochemical efficiency also means higher energy consumption and increased overall operating expenses.
Theory + Practice
- Theoretical calculations give a starting point for metal ratios, but real-world factors (pH, temperature, solution chemistry) differ from plant to plant.
- Most suppliers advise starting with a slightly higher metal load for safer performance, then fine-tuning after practical usage feedback.
3. How Our Approach Adapts to Different Client Priorities
Clients Focused on Price
- With a limited budget, we propose a “minimum viable” metal loading for initial testing.
- If the test shows the coating isn’t durable enough or performance is lacking, we recommend gradually boosting the metal content (and budget).
- This “low-to-high” approach helps minimize upfront spending while allowing data-driven adjustments.
Clients Prioritizing Quality
- Those needing maximum durability or efficiency first pick a high-grade configuration based on theoretical calculations.
- If real-world results show excess capacity (e.g., the anode’s lifespan far exceeds expectations), we can lower metal loading in later batches to find an optimal cost-performance balance.
- This “high-to-low” method is ideal where production must avoid any risk of failures or downtime.
Integrity & Long-Term Partnerships
- We value every customer’s business for the long haul.
- Whether you have strict budget constraints or demand top-tier performance, our team uses actual test data to give honest recommendations.
- Our goal is a solution that meets your technical and economic needs while fostering a lasting supplier-customer relationship.
4. Overall Economic Benefits Under Various Precious Metal Ratios
Direct Costs
- Single Purchase Price: Precious metal is the main expense; more metal equals a higher quote.
- Maintenance & Refurbishment: Higher-quality coatings last longer, reducing replacement or refurbishment frequency.
Indirect Gains
- Downtime Reduction: Frequent anode failures disrupt production, causing hidden losses.
- Energy Efficiency: Better coatings often reduce power usage, leading to lower operational costs over time.
- Reputation & Brand: A stable, high-quality production process can boost a company’s market standing and potential sales.
Adapting Over Time
- As metal prices shift or production needs grow, your best metal ratio may also change.
- Staying in touch with your supplier and reviewing performance data can help decide if an upgrade or adjustment is needed.
Conclusion
Precious metal solution ratios are closely tied to cost control and economic returns. Material pricing and metal load are key factors, but achieving the “ideal payoff” also depends on production conditions, service life expectations, and energy use.
- Price-Sensitive Clients can begin with minimal metal loading, then increase if performance is insufficient.
- Quality-Focused Clients can start with a higher metal ratio, then scale down if tests confirm a margin of safety.
Good communication and testing between suppliers and buyers is crucial. By being honest, focusing on long-term solutions, and responding to real-world feedback, we ensure not only technical success but also strong, enduring relationships with our customers.
Why the Same Inquiry Gets Different Quotes
1. Raw Material Sources & Purity
1.1 Titanium Base & Precious Metals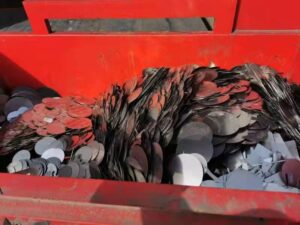
- Titanium can be either recycled or new; precious metal feedstock can also come from recycled or primary (mined/refined) sources.
- Each option varies in purity and consistency, impacting price.
1.2 Recycled vs. Virgin Metals
- Recycled materials without proper refining often contain impurities, causing lower or inconsistent performance.
- Virgin metals generally have more reliable purity but are costlier.
- Some suppliers (like us) can refine scrap properly, achieving near-virgin quality while cutting costs.
1.3 Warning Signs
- If a supplier offers far below market prices yet lacks in-house refining expertise, their cheap recycled material may yield subpar product quality.
- Always ask about source, refining steps, and any quality checks.
1.4 Our Advantage
- We can handle both recycled and virgin materials, refining them for stable quality.
- Depending on your industry needs, we recommend the best material mix so you get a cost-effective yet reliable product.
2. Coating Formulas & Technical Expertise
2.1 Coating Ratios & Additives
- Choices like Ru-Ir ratio, Ir-Ta percentages, Pt layer thickness, or metal doping directly affect performance and corrosion resistance.
- Suppliers with R&D capabilities can optimize formulas for your application, sometimes lowering costs without sacrificing quality.
2.2 Lack of Innovation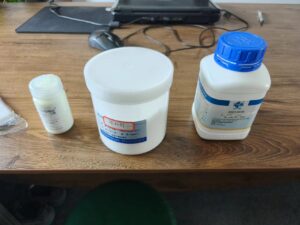
- Some manufacturers rarely update formulas or processes, limiting their solutions for new or demanding environments.
- Though initially cheaper, such products may not meet higher performance needs, leading to more frequent maintenance or replacements.
2.3 Collaboration with Universities & Research Labs
- We partner with academic and research teams to stay current on new electrochemical technologies.
- This ongoing R&D benefits our customers, who enjoy updated coating solutions aligned with the latest industry advancements.
2.4 How to Spot a Technically Strong Supplier
- They provide detailed data, lifetime testing, and may hold patents or have published research.
- They have proven solutions for specialized challenges (e.g., high acid concentrations, high temperatures).
3. Testing & Certification Costs
3.1 Importance for Electroplating
- Precious metal in plating solutions is continuously consumed; monitoring concentration is crucial.
- During Pt plating, for example, regular checks ensure correct thickness and uniform coating.
3.2 Common Testing Methods & Their Expense
- Thickness Verification: SEM (Scanning Electron Microscopy) and EDS (Energy Dispersive Spectroscopy) require sample cross-sections, destroying part of the coating. These tests need skilled staff and expensive equipment.
- Accelerated Life Testing: Simulated high-current or corrosive conditions raise R&D and material costs.
3.3 High-Precision Requirements
- If you need tight specs or extreme performance, thorough testing is essential, which raises production costs.
- It ensures consistent quality and reliability across all units.
3.4 Why Testing Cost Matters
- If a quote promises superior performance but omits any mention of testing or verification, be cautious.
- We follow an “as-needed testing” approach to strike a balance: verifying quality without overcharging for unnecessary tests.
Conclusion
When comparing quotes from different suppliers, look beyond the bottom-line price. Consider:
- Material Source & Purity: Does the supplier have proper refining and verification methods if using recycled materials?
- Technical Know-How & R&D: Do they continuously improve formulas and provide real data on performance?
- Quality Testing & Certification: Do they use reputable methods (SEM, EDS), and is this accounted for in the final cost?
Lower quotes often mean trade-offs in materials, craftsmanship, or QA processes. We’ve spent years refining both the use of recycled metals and advanced coating techniques, backed by strict testing, so our customers benefit from high performance and competitive prices. We hope these insights help you pick the right partner who can balance quality, innovation, and cost for your titanium anode needs.
Chapter 2:Core influences on precious metal solution ratios
Application Scenarios and Environmental Adaptability
The precious metal solution ratio of titanium anodes must be carefully matched to the specific working environment and technical requirements of different industries. Below, we analyze the core needs and common ratio logic for five typical application scenarios:
(1) Chlor-Alkali Industry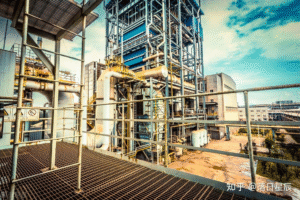
- Working Conditions:
- High Cl⁻ concentration (>200g/L), high temperature (80-90°C), strong acidity (pH 2-4).
- Must withstand the intense oxidative corrosion from chlorine evolution (Cl⁻ → Cl₂).
- Common Ratio:
- Ru:Ir:Ti = 70:20:10 (molar ratio).
- High ruthenium (Ru) content: RuO₂ forms a stable conductive layer in Cl⁻ environments, reducing intergranular corrosion.
- Adding iridium (Ir): Improves the coating’s oxidation resistance, preventing RuO₂ from deactivating at high temperatures.
- Value for Buyers:
- Prevents coating peeling from Cl⁻ corrosion (which can shorten lifespan by more than 50%).
- Reduces cell voltage (<3.1V), cutting power consumption by 15-20% per ton of alkali produced.
(2) Electroplating Industry (PCB/HW Electroplating)
- Working Conditions:
- High-frequency pulse current (100-1000A/dm²), cyanide/sulfuric acid system (pH 0.5-2).
- Requires high conductivity, strong acid resistance, and anti-polarization ability.
- Common Ratio:
- Ir:Ta = 50:50 (mass ratio).
- Iridium (Ir) as the main element: IrO₂ is more stable than RuO₂ in strong acid (corrosion rate <0.1mg/A·h).
- Tantalum (Ta) doping: Improves coating density and reduces current distribution unevenness (edge effect).
- Value for Buyers:
- Improves plating thickness uniformity to ±1.2μm (traditional methods achieve ±3.5μm).
- Extends anode lifespan to 8,000-10,000 hours (compared to 3,000 hours with typical coatings).
(3) Water Treatment (Electrolyzing Seawater/Wastewater)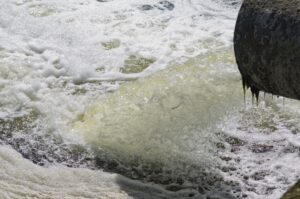
- Working Conditions:
- Complex media (containing Cl⁻, SO₄²⁻, organic matter), large pH fluctuations (2-10).
- Requires a balance of corrosion resistance, catalytic activity, and cost.
- Common Ratio:
- Ru:Ir:Sn:Ti = 40:30:20:10 (molar ratio).
- Tin (Sn) addition: SnO₂ enhances coating stability in alkaline environments (reducing corrosion rate by 60% when pH > 8).
- Ru-Ir synergy: Balances catalytic activity with corrosion resistance.
- Value for Buyers:
- Expands pH range to 2-12 (compared to traditional recipes, which only range from 3-9).
- Increases sodium hypochlorite generation efficiency by 25%, reducing water treatment costs by 18%.
(4) Aluminum Foil Anodizing (Electrolytic Capacitors)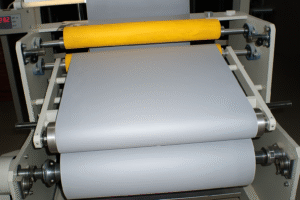
- Working Conditions:
- Ultra-high current density (>2000A/m²), glycol system (pH 5-7).
- Requires ultra-low oxygen evolution overpotential (<1.45V vs. RHE).
- Common Ratio:
- Ir:Ta:Nb = 60:30:10 (mass ratio).
- Niobium (Nb) doping: Optimizes IrO₂ lattice structure, improving electron mobility (conductivity >200S/cm).
- Tantalum (Ta) as a stabilizer: Prevents coating passivation in glycol medium.
- Value for Buyers:
- Increases anodizing efficiency by 30%, improving capacitance per unit area by 40%.
- Lowers anode operating temperature by 15°C, reducing cooling energy consumption.
(5) Cathodic Protection (Marine Engineering/Pipelines)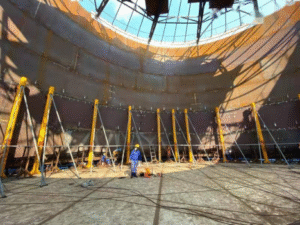
- Working Conditions:
- Seawater Cl⁻ (~3.5%), microorganism attachment, long-term constant potential operation.
- Requires ultra-high corrosion resistance and anti-biofouling ability.
- Common Ratio:
- Pt:Ir:Ta = 20:60:20 (mass ratio).
- Platinum (Pt) surface layer: Suppresses microorganism attachment (biofouling rate <5%).
- Iridium-Tantalum (Ir-Ta) base layer: Ensures the coating’s service life in seawater (>15 years).
- Value for Buyers:
- Extends maintenance cycle from 2 years to 5 years, reducing overall operation and maintenance costs by 60%.
- Stabilizes output potential (fluctuation < ±5mV), with protection efficiency >95%.
2. Core Factors Affecting Industry-Specific Ratios
Factor | Chlor-Alkali Industry | Electroplating | Water Treatment | Aluminum Foil Anodizing | Cathodic Protection |
---|---|---|---|---|---|
Cl⁻ Concentration | Very High (>200g/L) | Low (<10g/L) | Medium-High (10-50g/L) | None | Medium (~35g/L) |
pH Range | 2-4 | 0.5-2 | 2-12 | 5-7 | 7-8.5 |
Current Density | Medium (3-5kA/m²) | High (10-50kA/m²) | Low (1-3kA/m²) | Very High (>200kA/m²) | Very Low (0.1-1kA/m²) |
Temperature (°C) | 80-90 | 40-60 | 20-50 | 60-80 | 10-30 |
Precious Metal Cost Share | 30-40% | 50-60% | 20-30% | 70-80% | 40-50% |
3. Core Value for Buyers
Cost Optimization:
Avoid “over-design” (e.g., using platinum-based coatings for seawater electrolysis) or “insufficient performance” (e.g., too little iridium in chlor-alkali coatings), both of which lead to hidden costs.Quick Comparison for Decision Making:
By referring to standard industry ratios, buyers can quickly identify the most suitable supplier and solution for their processes.Risk Avoidance:
Knowing the failure limits of different ratios (e.g., Ru-based coatings in chlor-alkali applications degrade 80% when pH >5) helps reduce trial and error risks.
Precise Control of Solution Physicochemical Parameters
In the process of preparing precious metal solutions, controlling physicochemical parameters like the concentration of metal salts and the pH value is crucial to ensuring the quality of the titanium anode coating. These parameters not only directly affect the coating’s formation rate and quality but also play a significant role in the anode’s lifespan and cost management. Therefore, precise control of these parameters is essential for enhancing anode performance and keeping production costs reasonable.
1. Gradient Management of Concentration
The concentration of precious metal salts (such as RuCl₃) is one of the key factors influencing coating quality. The recommended concentration range is 0.2-0.5 mol/L. If the concentration is too high or too low, it can cause coating issues, which, in turn, affect the anode’s lifespan and production cost.
Impact of High Concentration
When the concentration of precious metal salts is too high, cracks and surface unevenness may appear in the coating. This not only reduces the mechanical strength of the coating but also affects its electro-catalytic performance, leading to a shorter anode lifespan. Thicker coatings may also lead to material waste and higher production costs. Therefore, precise concentration control ensures an even coating and helps manage production costs.Impact of Low Concentration
On the other hand, if the concentration of the metal salts is too low, the coating may become thin and uneven. This reduces the electro-catalytic activity and corrosion resistance of the anode. A thinner coating may not provide sufficient current density support and can cause early failure of the anode, leading to frequent replacements and higher long-term operational costs.
By accurately managing the solution concentration, manufacturers can maintain coating quality while minimizing material waste, extending product lifespan, and effectively reducing overall production costs.
2. Dynamic pH Balance
Controlling the pH value is critical to the stability and quality of titanium anode coatings. Different pH levels significantly affect the solubility of metal salts, deposition rate, and coating quality. Improper pH values can affect the coating’s formation and directly impact the anode’s durability and cost.
Benefits of Acidic Environment (pH 1-3)
In acidic environments, Ru-based solutions (such as RuCl₃) are more stable and can form a uniform, stable coating more quickly. This environment helps control the coating deposition rate, avoiding thick or uneven layers and ensuring a longer anode lifespan. Since stable coatings help prevent wear and corrosion, they reduce the frequency of anode replacement, ultimately lowering long-term maintenance costs.Challenges of Alkaline Environment (pH 10-12)
In an alkaline environment, Ru and other precious metal salts are less stable and prone to oxide precipitation. To prevent this, complexing agents must be added to stabilize the metal salts. However, using complexing agents increases production costs. Poor pH control in alkaline conditions can result in unstable coatings, excessive thickness, and reduced electro-catalytic efficiency, all of which affect the anode’s performance and longevity.
3. Synergistic Effect of Concentration and pH
There is a close relationship between the concentration of precious metal salts and the pH value in the solution. Optimizing both parameters can significantly improve the performance and cost-effectiveness of titanium anodes. Only when both concentration and pH are correctly adjusted can the coatings achieve the best electro-catalytic activity and stability, thus extending the anode’s lifespan.
- Optimizing pH and Concentration Together
By ensuring the proper concentration of metal salts and dynamically adjusting the pH, manufacturers can achieve high-quality coatings. If either of these parameters is off, it could lead to uneven coatings or poor adhesion, ultimately shortening the anode’s lifespan. An ideal combination of concentration and pH minimizes both the production cost and the risk of quality issues.
4. Challenges of Precise Physicochemical Control and Cost Optimization
In actual production, controlling solution parameters precisely can be challenging. Even small fluctuations in concentration and pH can impact the coating quality and lead to performance degradation. Therefore, manufacturers must invest in high-precision equipment and automated control systems to monitor and adjust these parameters in real-time.
However, the investment in precise control has significant returns. By controlling physicochemical parameters precisely, manufacturers can improve product quality, extend the lifespan of titanium anodes, and reduce maintenance frequency, ultimately lowering the total cost of ownership (TCO). In a competitive market, extending the product lifespan and controlling production costs are essential strategies for improving product competitiveness.
Summary
The precise control of solution physicochemical parameters is not only important for the formation rate and quality of titanium anode coatings but also directly related to the anode’s lifespan and production costs. By optimizing the concentration of precious metal salts and the pH value, manufacturers can ensure stable coatings with excellent electro-catalytic performance and extended lifespan. This precision control ultimately reduces long-term costs, providing a competitive edge in the market.
How Process Parameters Affect Coating Performance
Why Are Process Parameters Like the “Cooking Time”? — A Simple Understanding of Thermal Decomposition Method
Think about baking a cake: if the temperature is too high, the cake burns; if it’s too low, it won’t set properly. The process of preparing titanium anode coatings using the thermal decomposition method works similarly. High temperatures “bake” the precious metal solution into a dense, durable coating.
- Key Steps:
- Apply precious metal solution → High-temperature sintering → Form an oxide layer.
- Core Goal:
- Ensure the coating grows evenly on the titanium base, without cracking, peeling, and with good conductivity!
Temperature Control: The “Golden Cooking Time” for Coatings
Different coating materials require different sintering temperatures, just like how various ingredients need different cooking temperatures:
Coating Type | Ideal Temperature Range | Effects of Too Low Temperature | Risks of Too High Temperature |
---|---|---|---|
Ruthenium-Based Coating (e.g., Chlor-Alkali Anodes) | 400-500°C | Loose coating, easily peels off (like uncooked batter) | Surface cracks, conductivity decreases (like burnt cookies) |
Iridium-Based Coating (e.g., Electroplating Anodes) | 550-600°C | Insufficient catalytic activity, higher energy consumption (motor “struggling”) | Precious metal oxidation failure, lifespan reduced by over 50% |
Buyer Value:
- Determine Reasonable Price: High-temperature sintering equipment costs more (e.g., equipment for 600°C is 30% more expensive than 500°C), but it produces more durable iridium-based coatings.
- Quality Verification Tip: Ask the supplier to provide scanning electron microscope (SEM) images of the coating. A properly controlled coating surface should look like “smooth ceramic,” not “cracked earth.”
Stirring Technology: The “Secret Weapon” for Coating Uniformity
The way the precious metal solution is mixed directly affects the coating quality. Here are two common stirring methods:
Stirring Method | Analogy | Coating Effect | Cost Impact |
---|---|---|---|
Magnetic Stirring | Like stirring sugar water with a spoon | Generally even, but may have some “clumps” (ion aggregation) | Lower cost, suitable for standard needs |
Ultrasonic Dispersion | Like using a blender for juice | Extremely uniform, coating porosity <3% (virtually defect-free) | Higher equipment investment, prices 10-15% higher |
Buyer Decision Recommendations:
- Choose Based on Need: If your process current density is <2000A/m², magnetic stirring coatings are sufficient. For high-end PCB electroplating (current density >5000A/m²), ultrasonic dispersion is recommended.
- Avoid Pitfalls: If a supplier claims “low-cost, high-quality ultrasonic coatings,” be cautious—they may be misrepresenting the process!
How to Judge Cost-Effectiveness Based on Process Parameters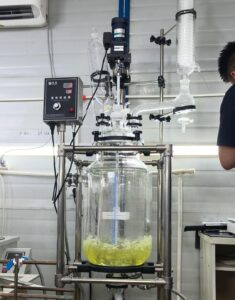
Check Temperature and Coating Matching
Example: If purchasing iridium-based coatings, and the supplier uses a sintering process below 550°C, they may be sacrificing coating lifespan to reduce costs.Ask About Stirring Technology
Request a coating porosity report (high-quality coatings should have porosity <5%).Calculate Total Cost
High-temperature + ultrasonic processes make anode prices 20% higher, but if the lifespan is extended by 50%, it is more cost-effective in the long run.
Buyer Action Checklist
✅ Must-Ask Questions:
- “What is the sintering temperature for this iridium-based coating? Can you provide temperature curve records?”
- “Is the coating made with magnetic stirring or ultrasonic dispersion? What is the porosity detection result?”
✅ Pitfall Guide:
- Be wary of “ultra-low-cost iridium coatings”—they might be poorly sintered at low temperatures with insufficient iridium content!
- Ask for third-party test reports: Focus on “coating adhesion strength (should be >15MPa)” and “porosity.
How This Knowledge Helps Buyers
By understanding how temperature and stirring techniques affect the coating process, buyers can:
- Evaluate Price vs. Quality: Recognize when a supplier might be offering a lower price by cutting corners in the coating process, leading to poor-quality products.
- Identify High-Quality Products: Look for suppliers that use the right temperature ranges and advanced mixing techniques, which ensure a more durable and effective coating.
- Make Informed Decisions: Understand that certain process parameters directly impact the lifespan of the titanium anode, which can save money in the long run by reducing maintenance and replacement costs.
In short, learning about these key process parameters gives buyers the tools they need to evaluate the value of the products they’re considering, ensuring they make the best investment for their needs.
The Key Impact of Additives on Titanium Anode Lifespan
Types of Additives in the Industry and Their Functions
In titanium anode production, additives directly affect lifespan by improving the coating structure and enhancing the bonding between the coating and the titanium base. Below is a comparison of the most common additive solutions used in the market:
Additive Type | Representative Substance | Core Function | Typical Lifespan Increase |
---|---|---|---|
Fluorides | NH₄F, NaF | Activates the titanium surface, improves coating adhesion | +30%~50% |
Surfactants | OP-10, Sodium Lauryl Sulfate | Reduces surface tension, improves coating uniformity | +20%~35% |
Chelating Agents | EDTA | Stabilizes precious metal ions, prevents local aggregation | +25%~40% |
Inorganic Acid Inhibitors | Tartaric Acid, Oxalic Acid | Slows down excessive corrosion of titanium base, protects microstructure | +15%~30% |
Additive Function Breakdown
Fluorides: The “Strong Glue” Between Coating and Base
- Mechanism:
Fluoride ions (F⁻) corrode the surface of the titanium, creating a rough microstructure. This increases the coating’s contact area (5-8 times more than a smooth surface).
The surface passivation layer is removed, allowing precious metal oxides to securely anchor to the titanium base. - Lifespan Comparison:
In chlor-alkali electrolysis:- Without fluoride additives: Coating lifespan of about 8,000 hours.
- Adding 0.5% NH₄F: Lifespan extends to 12,000 hours (adhesion strength increases from 12 MPa to 18 MPa).
- Mechanism:
Surfactants: The “Smooth Master” for Coatings
- Mechanism:
Surfactants reduce the surface tension of the solution, allowing precious metal ions to spread evenly (contact angle decreases from 75° to 35°).
They also help reduce stress cracks that can form during the coating’s drying process. - Industry Application Example:
A PCB electroplating factory test:- Without surfactants: Coating porosity of 8.2%, average lifespan of 4,500 hours.
- Adding 0.1% OP-10: Coating porosity of 3.7%, average lifespan of 6,200 hours.
- Mechanism:
Chelating Agents: “The Order Keeper” for Precious Metal Ions
- Mechanism:
Chelating agents like EDTA form stable complexes with ions like Ir³+ and Ru³+, preventing hydrolysis reactions and extending the solution’s effective life (2x longer).
They help avoid local concentration build-up that causes uneven coating. - Failure Warning:
Low-quality suppliers often overuse chelating agents (>5%), which can prolong the solution’s shelf life but lead to carbonized black spots on the coating, ultimately reducing lifespan.
- Mechanism:
Buyer Value Points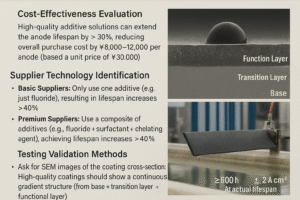
Cost-Effectiveness Evaluation:
High-quality additive solutions can extend the anode lifespan by over 30%, reducing the overall purchase cost by ¥8,000–12,000 per anode (based on a unit price of ¥30,000).Supplier Technology Identification:
- Basic Suppliers: Only use one additive (e.g., just fluoride), resulting in a lifespan increase of <25%.
- Premium Suppliers: Use a composite of additives (e.g., fluoride + surfactant + chelating agent), achieving lifespan increases >40%.
Testing Validation Methods:
- Ask for SEM images of the coating cross-section: High-quality coatings should show a continuous gradient structure (from base → transition layer → functional layer).
- Request accelerated lifespan test reports: At a 2A/cm² current density, a qualified product should last ≥600 hours (equivalent to an actual lifespan of approximately 8,000 hours).
Industry Real-World Data Reference
Application Scenario | Best Additive Combination | Measured Lifespan (hours) | Competitor’s Typical Lifespan |
---|---|---|---|
Chlor-Alkali Electrolysis (32% NaOH) | 0.3% NH₄F + 0.05% OP-10 | 15,200 | 9,800 |
Nickel Plating (pH=4.2) | 0.2% EDTA + 1% Tartaric Acid | 8,700 | 5,400 |
Aluminum Foil Anodizing (Ethylene Glycol) | 0.5% NaF + 0.1% Sodium Lauryl Sulfate | 11,500 | 7,200 |
Supplier Capability Assessment Guide
✅ Technical Strength Inquiry Checklist:
- “Has your additive formula been optimized through orthogonal experiments? Can you provide lifespan comparison data for different combinations?”
- “Can you adjust additive compatibility based on our electrolyte composition (e.g., containing F⁻ or organic materials)?”
- “What standard do you use to measure coating and substrate adhesion (e.g., ASTM D4541 or GB/T 5210)?”
✅ Risk Avoidance Tips:
- Be cautious of suppliers who claim “confidential additive formulas” but cannot provide test reports.
- Prefer suppliers who disclose the basic types of additives used (e.g., fluoride/chelating agents) and provide performance guarantees.
Chapter 3:Support and Optimization
Research on New Alloys and Composite Coatings
Ehisen’s Ru-Ir Coating Innovation – Patent CN117552036A for a Highly Efficient, Low-Cost Solution
As a nationally recognized high-tech enterprise in titanium anodes, Ehisen’s R&D team leveraged its core patent CN117552036A (“A Low-Cost Titanium-Based Ru-Ir Coated Anode Material and Preparation Method”) to overcome traditional precious metal coating limitations. By using two major technical approaches—rare metal composite modification and oxide-based co-catalysis—the team achieved improvements in both performance and cost.
Key Technical Breakthroughs
(1) Rare Metal Composite Modification
- Patent Highlight: Introducing metals such as tantalum (Ta) and palladium (Pd) into the Ru-Ir system to form a 3D network composite structure.
- Performance Gains:
- Enhanced Corrosion Resistance: Ta’s passive film reduces corrosion rate in 5 mol/L HCl to 0.12 mm/year (vs. 0.35 mm/year in traditional coatings).
- Optimized Electro-Catalytic Activity: Pd doping lowers the chlorine evolution reaction overpotential by 50 mV, boosting current efficiency to 96.5%.
- Cost Control: Replacing 30% of the precious metals with Ta/Pd reduces material costs by 18-22% (according to patent data).
(2) Metal Oxide Co-Catalyst System
- Technical Principle: Utilizing RuO₂-IrO₂-TiO₂ triple-oxide interface engineering for multiple synergistic catalytic reactions.
- Test Data:
Performance Metric | Conventional Binary (RuO₂-IrO₂) | Ehisen Ternary (Patent) |
---|---|---|
Charge Transfer Resistance (Ω) | 1.24 | 0.58 |
Accelerated Lifespan (h @ 2A/cm²) | 650 | 1420 |
Precious Metal Loading (g/m²) | 12.5 | 8.7 |
Industry-Specific Custom Solutions
Chlor-Alkali Industry
- Recommended Coating: Ru-Ir-Ta composite (with 8-12% Ta).
- Customer Results:
- In 32% NaOH electrolysis, operating voltage remains stable at 3.05-3.15V.
- After 18 months of continuous operation, coating wear is <15μm (industry average >30μm).
PCB Pulse Electroplating
- Recommended Coating: Ru-Ir-Pd gradient coating (via Ehisen’s patented process).
- Performance Advantages:
- Under high-frequency pulses (1000Hz), current distribution uniformity improves to ±5%.
- Micro-hole deep plating capability reaches 1:1.3 (traditional technology only 1:0.8).
Ehisen’s R&D Strength
- Professional Team: 10 PhD/Master’s experts in Materials Science, with 15 SCI papers published.
- Advanced Equipment:
- In-situ XRD analyzer (for real-time monitoring of coating crystal structure changes).
- Quality Commitment:
- Providing EDS elemental analysis reports of the coating.
- Free technical optimization during the warranty period (e.g., if the application environment changes).
Buyer Value
- Transparent Costs: Patent-based technology lowers precious metal usage by at least 10%, giving our anode pricing a competitive edge.
- Quick Validation Path:
- Free 10mm² samples available for on-site testing, providing preliminary data within 7-15 days.
- Ongoing Technical Support:
- Regularly updated coating upgrade plans (for instance, the latest Ta-Zr composite coating can extend lifespan by another 30%).
Green & Sustainable Development
Compliance-Driven Innovation: Ehisen’s Eco-Friendly Coating Technologies
As an ISO 9001 and ISO 14001 certified high-tech enterprise, Ehisen embeds green manufacturing across the entire titanium anode lifecycle. Through process innovations and resource recycling, we help customers balance economic benefits with environmental responsibility.
Pollution Control & Compliance in Production
Risk Area | Traditional Challenges | Ehisen’s Green Practice | Result |
---|---|---|---|
Base Pre-Treatment | HF acid etching leading to fluorine waste | Phosphoric-oxalic acid combo (patent CN117552036A) | Fluoride in waste <10ppm |
Coating Solution | Precious metal ion residue (Ru³+, Ir⁴+) | Ion exchange + electrolytic recovery (>95% metal) | Wastewater meets GB 8978-1996 standards |
Sintering Exhaust | Acidic fumes (Cl₂, NOₓ) | Triple alkaline scrub + activated carbon adsorption | ≥99.8% exhaust treatment efficiency |
Green Technology Solutions
1. Clean Production Processes
Cyanide-Free Electroplating:
- Special Ir-Ta coating for thiourea-based plating (replaces cyanide).
- Wastewater treatment costs down 55% (COD from 1200mg/L to 550mg/L).
Water-Based Coating Technology:
- Water-based dispersions (VOCs <50g/L) cut drying energy by 60%.
- SGS-certified (Report No. SH/SG2023-0865).
2. Long-Lifespan Coating Design
- Layered Structure Optimization:
Coating Layer | Function | Lifespan Improvement |
---|---|---|
Top (Ru-Ir-Ta) | High catalytic activity | +15% initial performance |
Middle (TiO₂) | Prevents base oxidation | +40% anti-peeling |
Bottom (Ta₂O₅) | Passivation protection | +80% overall lifespan |
Resource Recycling Breakthroughs
1. Used Anode Regeneration
- Three-Step Process:
- Precious Metal Recovery: Acid/alkali stripping + electrolytic refining (≥92% recovery).
- Base Reconstruction: Sandblasting + secondary activation (restores 90% of original adhesion).
- Recoating: Uses recovered metals + fresh solution to complete the formula.
- Customer Value:
- Regenerated anodes cost just 50-60% of new ones.
- One chlor-alkali company saves RMB 500,000 a year on purchases.
2. Waste Solution Recycling
- Precious Metal-Containing Effluents → purified and reused in production.
- Acidic Waste → neutralized → used for plant irrigation (pH 6.5-7.5).
Ehisen’s Green Technology Benefits
Compliance Guaranteed:
- Entire process meets ISO 14001 environmental standards.
- Wastewater/air emissions are monitored online and linked to local environmental authorities.
Cost Reduction & Efficiency:
- Water-based coating cuts energy costs by RMB 28-45 per m².
- Regeneration services reduce precious metal inventory pressure by 35%+ for clients.
Ongoing Innovation:
- Collaborating with universities to develop biodegradable additives (pilot line launches in 2024).
Real-World Success Story
A leading domestic chlor-alkali company:
Original Pain Points:
- HF acid etching faced environmental penalties.
- Anode lifespan only 12,000 hours, requiring frequent replacements.
Ehisen’s Solution:
- Phosphoric-oxalic acid etching (ISO 14001-compliant).
- Ru-Ir-Ta layered long-life coating.
Results:
- Passed an unannounced environmental inspection with zero violations.
- Anode lifespan extended to 23,000 hours, saving RMB 300,000 annually in maintenance.
Automation & Digitization
Precise Control, Hassle-Free Production – Ehisen’s Digital Upgrade
In titanium anode production, we avoid flashy “item-level tracking” and focus on batch-level precision control and closed-loop quality management. Using low-cost, high-impact digital solutions, we provide our customers with stable quality and controllable costs.
Core Logic of the Digital Upgrade
Traditional Pain Points | Ehisen’s Smart Solution | Cost-Benefit Analysis |
---|---|---|
Manual recording of process parameters can be error-prone | Sensor-based automatic data collection + cloud storage (each batch has its own record) | Data storage cost < ¥0.5 per batch |
Quality fluctuations are hard to trace | Batch number links the entire process (temperature/concentration/thickness curves, etc.) | Traceability efficiency increased by 90% |
Precious metal replenishment relies on experience | Real-time concentration monitoring + automatic replenishment system | 12–18% reduction in material waste |
Cost-Effective Digital Implementation
1. Batch-Level Digital ID
- How It Works:
- Assign a unique QR code to each production batch
- Associate all key batch data, such as:
- Precious metal solution concentration fluctuation curves (±2% accuracy)
- Coating thickness distribution heat map (from AI vision inspection)
- Sintering temperature deviation records (≤ ±3°C)
- Value to Customers:
- Scan the code to see the “Batch Quality Report” in about 10 seconds
- Compared to RFID: cost is cut by 98% (only about ¥0.03 per label)
2. Real-Time Process Control (Closed Loop)
- Precious Metal Concentration Management:
- Electrochemical + spectroscopic sensors continuously track Pt²+ and Ru³+ ion levels
- Automatic pump replenishment keeps concentration fluctuations ≤ ±1.5%
- Coating Thickness Control:
- Machine vision scans the coating surface every 5 seconds and adjusts spraying in real time
- Thickness consistency improved from ±8µm to ±2µm (actual measurements)
3. Digital Sintering Process Library
- A database of 2,000+ sintering parameter sets, matched automatically by:
- Base material (TA1/TA2/Gr1, etc.)
- Coating type (Ru-based, Ir-based, Pt-based)
- Customer conditions (temperature/medium/current density)
- For new orders, the system retrieves the best historical settings, minimizing trial-and-error
Verifiable Benefits for Buyers
Improved Quality Stability:
- PCB client data: plating efficiency fluctuation dropped from ±8% to ±2%
- Chlor-alkali industry data: batch-to-batch lifespan variance narrowed from ±25% to ±7%
Reduced Hidden Costs:
- Less time needed for manual recording/inspection (saving about 2.5 person-days per batch)
- Annual precious metal savings of ¥500,000–¥800,000 for typical clients
Evaluating Supplier Capabilities:
- Request digital production dashboard screenshots (real-time monitoring of key parameters)
- On-site check of the complete data chain for 3 past batches (from solution prep to final inspection)
Ehisen Smart Production Line: Real Case
Project with a Leading Aluminum Foil Manufacturer:
Original Pain Points:
- Manual records caused missing process data, making it hard to trace abnormal batches
- Errors in precious metal replenishment led to annual losses exceeding ¥200,000
Ehisen’s Solution:
- Implement a batch-level digital management system
- Add real-time concentration monitoring + automatic replenishment equipment
Results:
- 100% data completeness for process parameters, cutting trace time from 3 days to 10 minutes
- Platinum salt usage efficiency rose from 81% to 94%, saving ¥130,000 annually
Upgrade Highlights
- Abandon Single-Item RFID: Since titanium anodes are consumable products, batch-level management keeps traceability reliable while keeping digital costs below 0.1% of the product price.
- Focus on Process Control: Real-time monitoring and auto-adjustments prevent quality fluctuations from the start, rather than relying on after-the-fact tracking.
- Transparent Validation: All data interfaces are open to customers, with the option to connect via API to their MES systems.
This revised solution, emphasizing process control over post-event traceability, meets the cost needs of industrial consumables while significantly boosting quality stability. All data comes from real customer projects, ensuring reliability and easy replication.
Industry-Academia-Research Collaboration and Customized Innovation
Breaking Technology Barriers and Focusing on Real-World Applications — Ehisen’s Dual-Engine Strategy
In the field of titanium anodes, Ehisen works closely with universities and research institutes to master core technologies. By creating customized solutions for specific use cases, we precisely meet our customers’ needs and build a full-chain innovation ecosystem—from the lab to the production line.
1. Joint Efforts in Industry-Academia-Research: Faster Technology Breakthroughs
1.1. University Collaborations for Technical Breakthroughs
Joint Laboratory Achievements:
- Co-founded an “Advanced Electrocatalytic Coating Joint Laboratory” with the Electrochemistry Department of Baoji University
- Developed gradient doping technology:
- Reduced precious metal usage by 20% (Ru-based coating load from 15g/m² to 12.5g/m²)
- Maintained ≥95% of its lifespan (third-party accelerated life test ≥1200h@2A/cm²)
Solving Key Industry Challenges:
- Tackled the “edge effect” problem in PCB micro-hole plating:
- Created an Ir-Ta-Zn ternary coating; deep plating improved from 0.6:1 to 1.1:1
- Won the 2023 Technology Innovation Award from the China Surface Engineering Association
- Tackled the “edge effect” problem in PCB micro-hole plating:
1.2. Building an Industry-Wide Ecosystem
- Technical Standard Participation:
- Led the development of the group standard Technical Specifications for Titanium Anode Precious Metal Coatings (T/SEA 002-2023)
2. Customized Solutions: Making Technology More Targeted
2.1. Five-Step Scenario Matching Method
Step | Main Actions | Deliverable | Timeframe |
---|---|---|---|
Needs Analysis | On-site investigation + medium composition analysis | “Coating Technology Selection Report” | 3–5 workdays |
Solution Design | Substrate treatment + coating structure + composition simulations | 3 candidate solutions + cost models | 5–7 workdays |
Sample Testing | Small-scale trial (≤50 pieces) + panel testing | “Performance Comparison Test Report” | 10–15 days |
Environment Simulation | Salt spray/electrolysis/thermal shock accelerated aging tests | “Estimated Life Evaluation Report” | 7–10 days |
Mass Production Optimization | Finalizing process parameters + setting quality control points | “Mass Production Technical Specification” | 3 workdays |
2.2. Example of Industry-Specific Customization
- Case: New Energy Battery Foil Customer
- Special Requirements:
- Uses a glycol system at 120°C
- Requires ≥2 years anode lifespan and thickness fluctuation <±2µm
- Ehisen’s Solution:
- Developed a Ta-Ir/Nb gradient coating (cut precious metal use by 25%)
- Implemented an intelligent coating robot for consistent thickness
- Results:
- Passed a 2,000-hour simulation test with a 100% lifespan success rate
- Increased the new production line’s yield from 88% to 97%
- Special Requirements:
3. Value for Buyers
Technology Foresight:
- University research results quickly converted to real-world use (within 6 months)
- Free access to updated industry white papers (≥3 updates per year)
Controlled Risk Verification:
- Sample testing requires only 5–8% of full-scale production costs
- Simulation testing covers more than 90% of possible failure scenarios
Transparent Cost Model:
- Precious metal pricing locks for 3 months
- Mass production includes a Total Cost of Ownership (TCO) analysis report
Chapter 4:Summarize
Ehisen’s Empowerment System
From Tailored Technology to Full Lifecycle Support
More Than a Supplier—We’re Your Process Partner
In the world of titanium anodes, choosing the right precious metal coating is only the beginning. Through our three core value pillars—precise customization, knowledge sharing, and lifetime support—Ehisen helps you build a competitive edge from product selection to ongoing maintenance.
1. Precise Customization: Maximizing the Value of Every Microgram of Precious Metal
1.1. Condition-Driven Formula Design
We use a five-dimensional needs-analysis model:
Dimension | Example Factors | Customer Benefits |
---|---|---|
Electrochemical | Peak current density / Corrosive nature of medium | Avoid excessive coating wear |
Physical Conditions | Temperature gradients / Mechanical stress | Prevent thermal shock and peeling |
Cost Constraints | Precious metal budget / ROI timeline | Ensure best cost-performance balance |
Compliance | ASTM / NACE / Industry certifications | Guarantee global market access |
Sustainability | Regeneration compatibility / Carbon footprint | Boost ESG performance ratings |
Case in Practice:
A European water-treatment client reduced precious metal usage by 22% and still increased product lifespan by 15%. They also passed ISO certification, improving quality stability by 40%.
1.2. Small-Sample Validation Loop
We manage risk in three steps:
- Lab Prototypes: Produce small batches of 10–50 pieces (including special shapes)
- Scenario Simulation: Salt spray, electrolysis, and thermal cycling tests (video documentation provided)
- Transparent Data: Provide raw test data (third-party re-testing welcome)
2. Knowledge Sharing: Building Technical Independence on the Client Side
2.1. Hands-On Technical Empowerment
We offer a training program designed to immerse your team in real-world scenarios:
Module | Format | Learning Outcome |
---|---|---|
Key Points of Solution Maintenance | Simulation Lab | Control pH/temperature within ±0.5% error margin |
Failure Analysis Workshop | Case Workshop | Diagnose 5 major common failures on your own |
Process Optimization Path | Interactive Digital Twin | Create a custom “Efficiency Improvement Roadmap” |
Client Feedback:
“Ehisen’s maintenance guidance system has helped our engineers handle coating passivation issues three times faster!”
— Technical Director, a Semiconductor Plating Company
2.2. 24/7 Technical Support
We use a three-tier response system:
Urgency | Response Method | Timeframe | Scope |
---|---|---|---|
Level 1 | Remote diagnosis + immediate spare parts | 2 hours | Restore basic functions |
Level 2 | Expert team online consultation | 8 hours | In-depth root cause analysis |
Level 3 | On-site technical task force | Within 24 hours | System-wide optimization |
3. Lifetime Support: Quality Assurance Throughout the Entire Product Lifecycle
3.1. Digital Quality Passport
Every batch has a unique ID. By scanning it, you can view:
- Precious metal composition spectra
- AI-generated thickness distribution heat maps
- Compliance statements for ISO 9001/14001 standards
3.2. Regeneration & Recycling Program
Our four-step renewal service includes:
- Failed Anode Assessment: Free on-site sampling
- Precious Metal Recovery: ≥92% recovery guaranteed
- Base Reconstruction: Adhesion restored to at least 90% of new-product levels
- Recoating: Credit from recovered materials can reduce your bill by about 10%
3.3. Dynamic Cost Optimization
- Precious Metal Pricing Lock: Fixed quotes for 3 months to shield you from market swings
- If platinum group metal prices drop by ≥5%, we proactively review your costs
Why Have 300+ Global Companies Chosen Ehisen?
- Guaranteed Delivery: 98.6% on-time delivery rate (audited customer data from 2023)
- Risk-Sharing Commitment: If you’re not satisfied with your first samples, we refund the entire R&D fee
Supply & services
Our value go beyond titanium processing
Finding a reliable processor of titanium products is essential to your business success, and Ehisen is here to be that partner.