Expert Solutions for Titanium Pickling and Immersion Treatments
At Ehisen, we specialize in providing advanced acid pickling and immersion treatments for titanium anodes, tailored to meet the demanding requirements of your projects. Whether for electroplating, water treatment, or electrolytic hydrogen production, our processes ensure optimal surface preparation, enhanced performance, and extended product lifespan. Our commitment to quality guarantees precision and reliability in every treatment we provide, catering to your industry-specific needs.
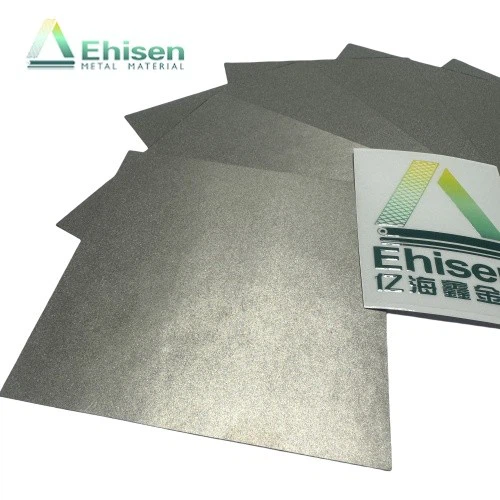
Titanium sintered plate
Our titanium sintered plates are characterized by a porosity of up to 35% and uniform particle distribution. Designed for applications in chemical processing, filtration, and electrolytic processes, these plates deliver consistent performance and mechanical stability under demanding conditions.
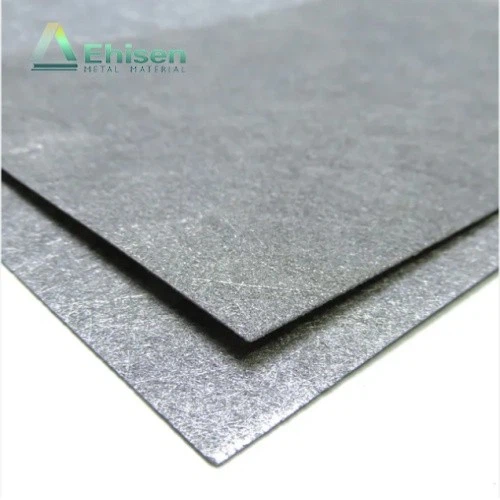
Titanium fiber felt
Our titanium fiber felt is crafted from cut or drawn fibers, with individual filaments measuring 20 µm in diameter. Available in multiple materials, we offer custom porosity and dimensions to meet the specific needs of fuel cells, filtration systems, and catalytic applications.
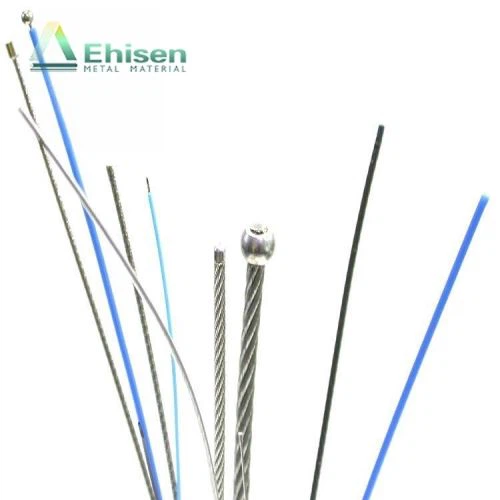
Titanium wire rope
Our titanium wire ropes are available in a variety of configurations, including 1*7, 7*7, and 7*19. Suitable for both medical and industrial applications, these ropes can be custom-manufactured to meet specific requirements, offering strength and durability in challenging environments.
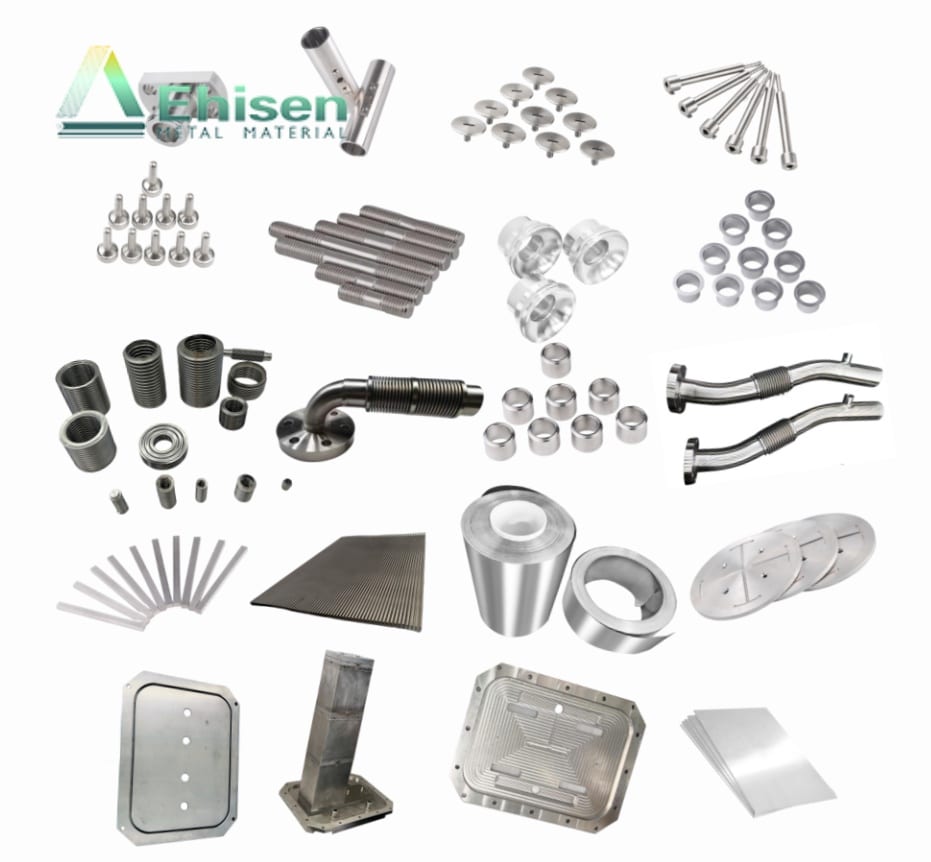
Titanium CNC machining parts
Our titanium CNC machined parts are produced using advanced five-axis machining centers and verified with 3D inspection equipment to ensure precision and accuracy. Designed for aerospace, medical, and industrial uses, these parts meet the highest standards of quality and reliability.
Diagram of Acid washing immersion treatment
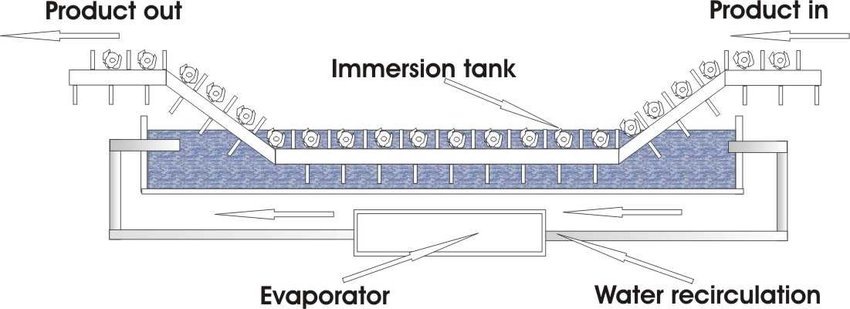
About Us
Why Choose Ehisen for Titanium Anode Pickling and Soaking?
At Ehisen, we specialize in efficient and reliable surface pre-treatment processes, ensuring titanium substrates are in the best condition for precious metal coating. Here are our key advantages:
Extensive Processing Experience
With years of experience in titanium anode production, we understand the requirements of various precious metal coatings. We adjust pre-treatment processes based on coating lifespan, application, and industry needs, offering tailored solutions for every client.
Real-Time Monitoring for Precision
Our advanced monitoring systems allow us to track the condition of pickling solutions in real time. This ensures precise adjustments to avoid over-treatment and maintain optimal surface quality.
Continuous Process Optimization
Our dedicated R&D team works to improve pickling and soaking methods continuously, providing clients with ongoing technical support for better performance and efficiency.
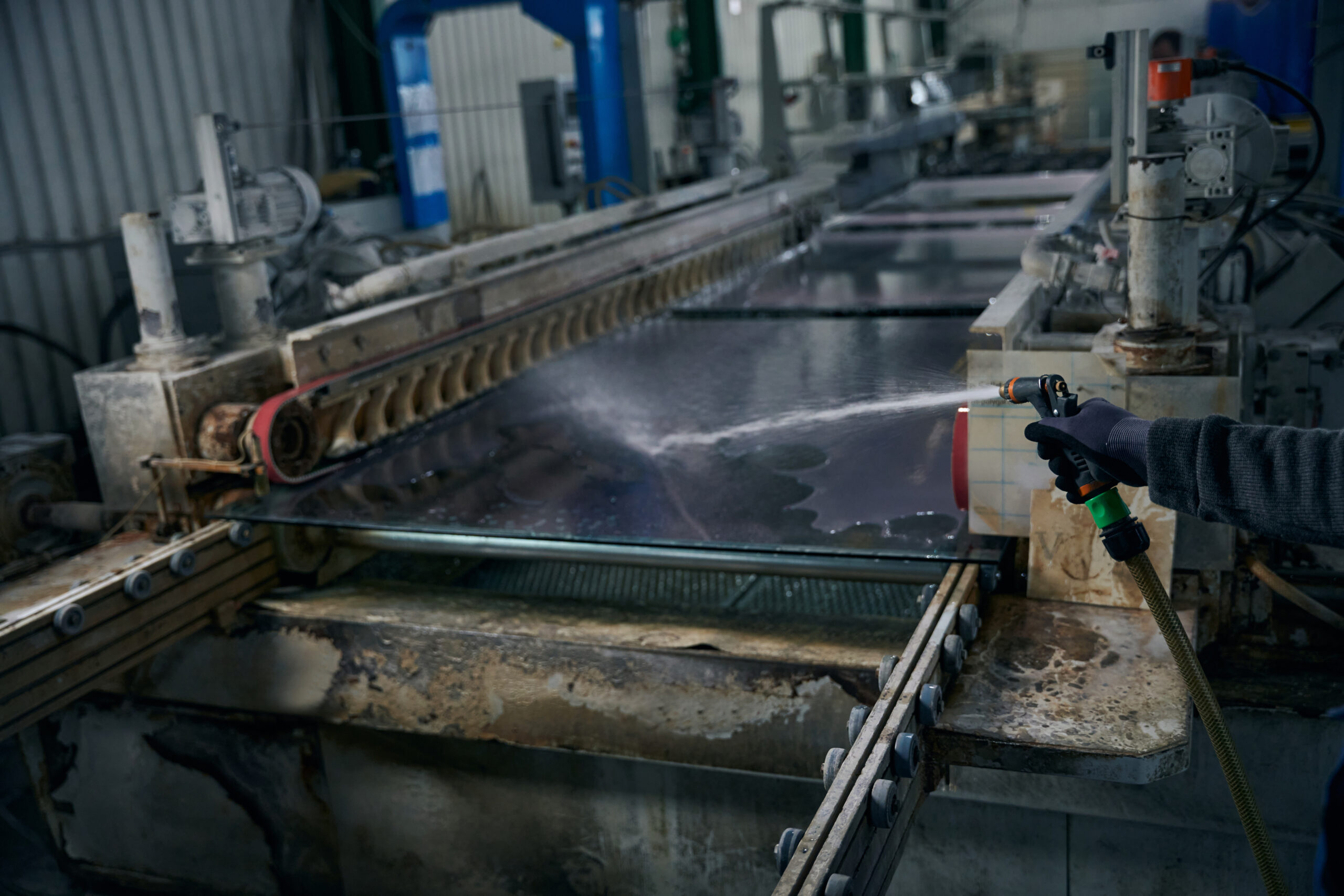
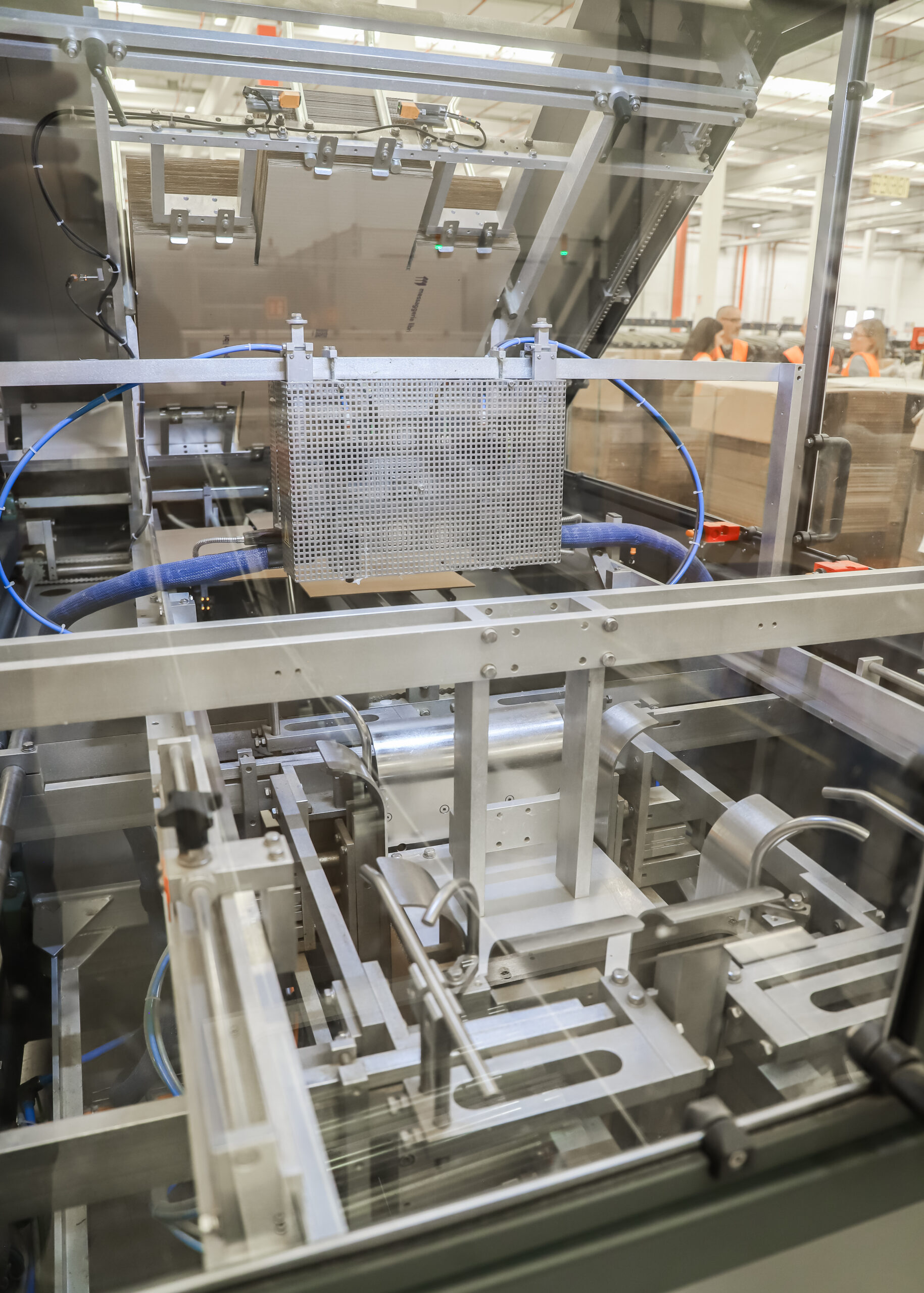
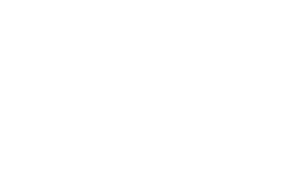
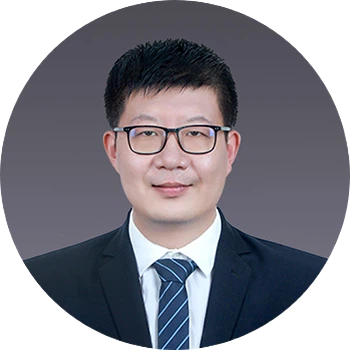
Dr. Miao
Technical Director of Ehisen
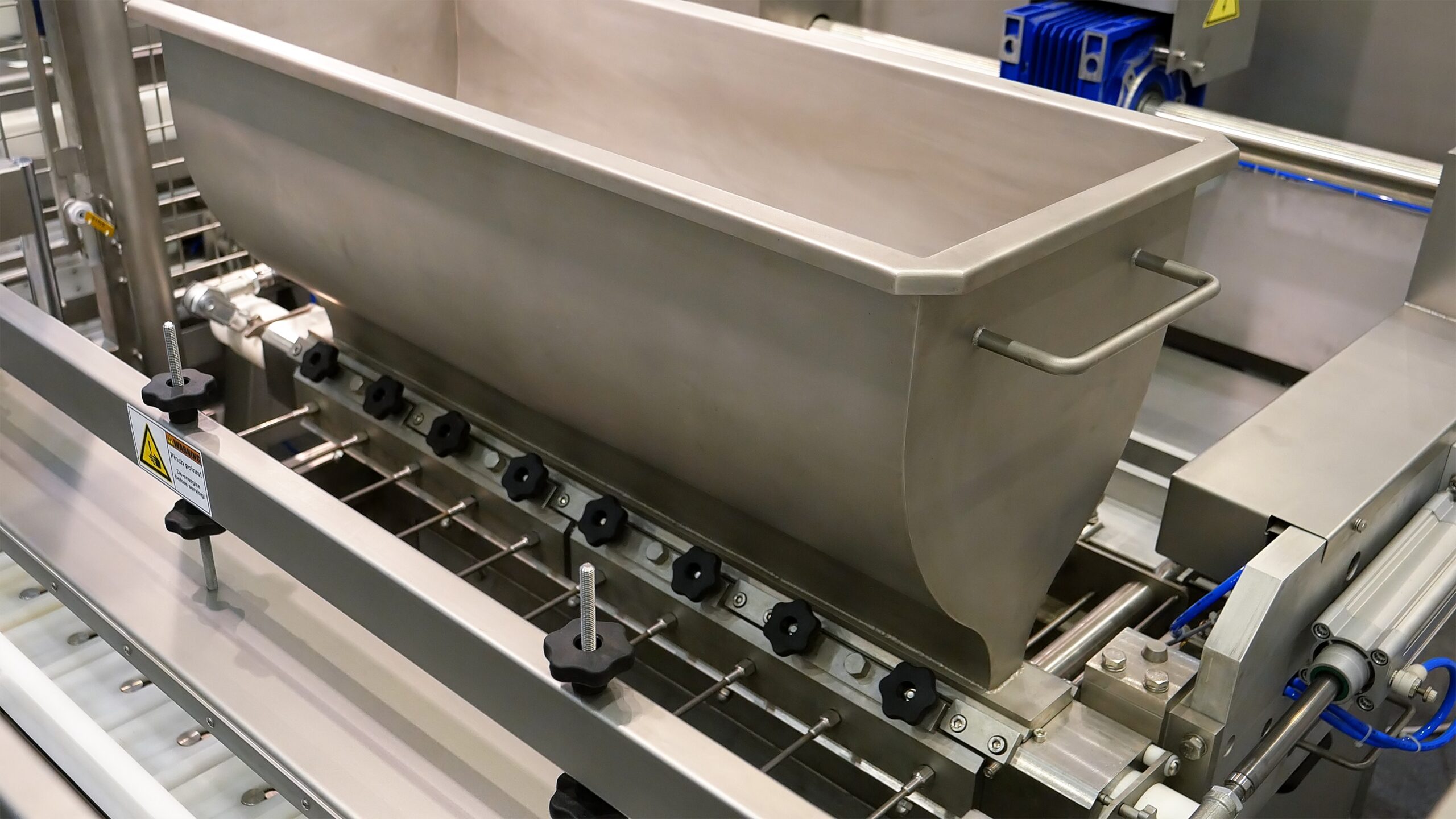
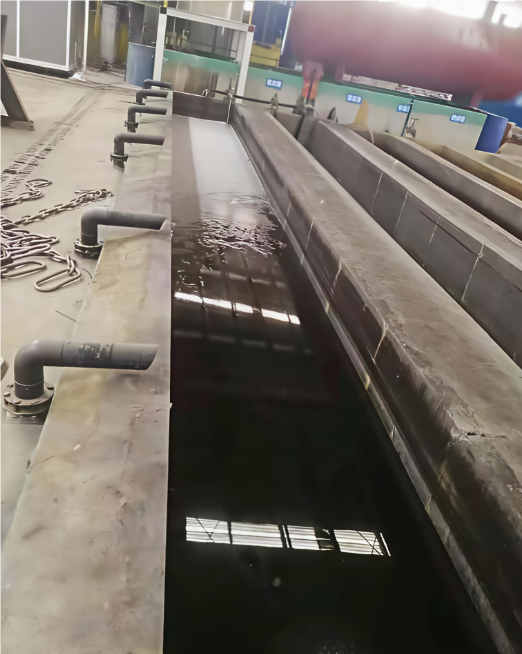
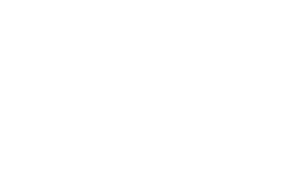
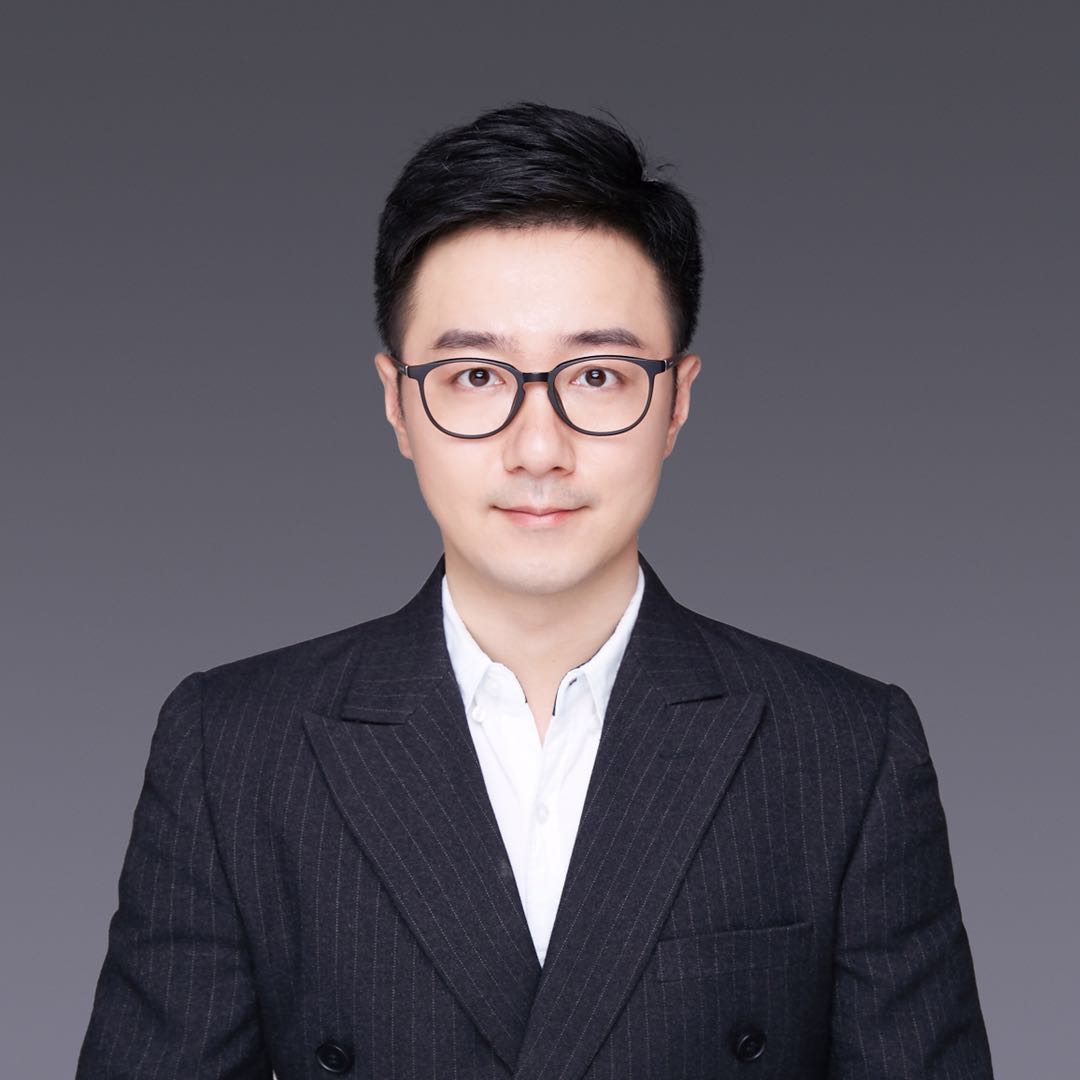
Spencer Xu
CEO of Ehisen
Seamless Production Integration
We control the entire pre-treatment process on our production lines. This ensures that pickling and soaking steps align perfectly with the timeline, maintaining the substrate’s ideal active state before precious metal coating begins.
Flexible Solutions for Unique Needs
For products with special surface treatment requirements or larger dimensions, we collaborate with trusted partners to handle complex or oversized processing tasks promptly.
Advanced Post-Treatment Preservation
When immediate coating is not possible, we use methods like soaking or vacuum sealing to preserve the titanium substrate. This ensures the surface remains suitable for the next step, meeting all processing requirements.
Why Mastering Titanium Pre-Treatment is Essential for Procurement Professionals
For procurement professionals in the titanium industry, understanding titanium pre-treatment processes like pickling and soaking is vital. These steps significantly influence the quality, lifespan, and performance of titanium anode products while also affecting project costs and timelines. At Ehisen, we analyze each project’s specific requirements to determine the optimal pre-treatment methods, adjusting processes based on substrate type, coating requirements, and application scenarios. This thorough approach ensures accurate cost estimates, smooth transitions to subsequent production stages, and reliable performance—empowering procurement professionals to assess value accurately and make strategic decisions.
Table of Contents
Chapter 1:Overview of Titanium Pickling and Soaking Process
Principles and Functions of Pickling and Soaking
In metal processing, pickling and soaking are key steps to improve surface quality. These processes not only enhance the appearance of the material but also directly affect its performance and lifespan. Below is a detailed explanation of the principles and benefits of pickling and soaking, along with their applications across different metals.
Basic Principles of Pickling and Soaking
- Pickling: A chemical process that uses acid solutions to remove oxides, impurities, and contaminants from metal surfaces.
- Soaking: Following pickling, this involves keeping the material in an acid bath for a certain time to ensure thorough and uniform surface treatment.
Functions of Pickling and Soaking:
Remove Oxide Layers: During high-temperature processing, titanium surfaces form dense oxide films that affect further processing and reduce corrosion resistance. Pickling effectively removes these layers to restore the metal’s original state.
Clean Impurities: Oils, cutting fluids, and other contaminants often remain on the surface after machining or storage. Pickling eliminates these residues, ensuring the surface is clean for processes like welding, coating, or plating.
Improve Surface Activity: A clean, slightly roughened surface enhances bonding in subsequent steps such as welding or coating, improving durability and efficiency.
Adjust Surface Texture: By controlling pickling parameters (acid concentration, temperature, time), the surface’s microstructure and roughness can be optimized for specific applications, especially for titanium anodes where surface properties impact performance and lifespan.
2.Comparison of Pickling Across Different Metals
The pickling and soaking process varies for different metals due to differences in acid media, treatment goals, and challenges.
Metal | Acid Media | Main Purpose | Challenges |
---|---|---|---|
Titanium | Nitric acid + hydrofluoric acid | Remove oxide layer, enhance activity | Control acid concentration and prevent over-corrosion |
Zirconium | Nitric acid + hydrofluoric acid | Oxide removal, weld preparation | High acid mist and strict safety requirements |
Nickel | Sulfuric acid, hydrochloric acid | Oxide and impurity removal | Avoid surface or intergranular corrosion |
Tungsten | Nitric acid, hydrofluoric acid | Oxide removal, surface refinement | Control immersion time to avoid excessive dissolution |
Molybdenum | Nitric acid, hydrofluoric acid | Oxide removal, burr removal | Narrow temperature range to prevent roughening |
3.Unique Benefits of Titanium Pickling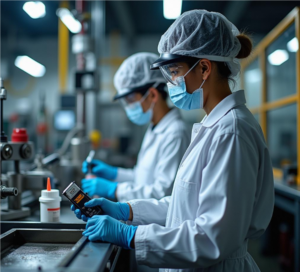
Titanium is widely used in harsh environments due to its exceptional corrosion resistance. However, these conditions often create thick oxide layers that are hard to remove. Professional pickling and soaking processes efficiently eliminate these layers while preserving the base material, maintaining titanium’s superior mechanical and corrosion-resistant properties.
4.Key Steps in Pickling and Soaking
Acid Preparation: The acid ratio depends on the metal. For titanium, a carefully calculated mix of nitric and hydrofluoric acids is used to ensure effective oxide removal without damaging the base metal.
Temperature Control: Reaction speed increases with temperature, but excessive heat may cause over-corrosion. Maintaining optimal temperature is crucial for consistent results.
Soaking Time: Proper soaking ensures complete oxide removal. Over-soaking can harm the base material, so the time must be optimized for the best results.
Surface Monitoring: Regular checks, such as visual inspection or pH monitoring, ensure stable and consistent process parameters.
Summary
Pickling and soaking are foundational steps in titanium surface treatment. A well-designed process significantly enhances the surface quality of titanium and other high-performance metals, ensuring superior performance in subsequent processing and applications.
Process Parameters and Workflow for Pickling and Soaking
1. Preparation of Pickling Solution
(1) Common Acids and Ratios
- Nitric Acid (HNO₃): Used for initial removal of oxide layers and surface cleaning. The concentration is typically 5%–15% (by volume), adjusted based on oxide thickness and production requirements.
- Hydrofluoric Acid (HF): Essential for removing tough titanium oxides and adjusting surface roughness. The concentration is usually 0.5%–5%. Higher concentrations can lead to excessive corrosion.
- Mixed Acids: A combination of nitric acid and hydrofluoric acid, sometimes with small amounts of hydrochloric acid or sulfuric acid, enhances the ability to remove stubborn oxides.
- Example ratios: Nitric Acid 10%–15% + Hydrofluoric Acid 1%–3%
- For thicker oxides or high-temperature residues, hydrofluoric acid can be increased to 3%–5%, but exposure time must be tightly controlled.
(2) Key Control Parameters
- Acidity (pH): Typically kept in a highly acidic range (pH 1–2 or lower) to ensure effective oxide removal.
- Oxidation-Reduction Potential (ORP): Some factories monitor ORP during pickling to assess oxide removal progress and adjust the acid ratio in real time.
2. Pre-Treatment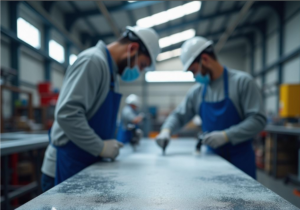
Pre-treatment is crucial for improving efficiency and avoiding interference during pickling:
Surface Cleaning/Degreasing
- Use alkaline cleaners or warm water to remove oils, fingerprints, and other contaminants.
- Cleaning time: 5–15 minutes, depending on contamination levels.
Mechanical or Chemical Oxide Removal (Optional)
- For thick oxides or severe burns, light sanding or blasting may be performed to reduce the pickling burden.
- Alternatively, a brief soak in a weak acid solution can soften oxide layers.
Inspection and Sorting
- Check for surface defects or weld areas to adjust soak time and acid concentration during pickling, preventing overcorrosion or localized damage.
3. Detailed Pickling and Soaking Process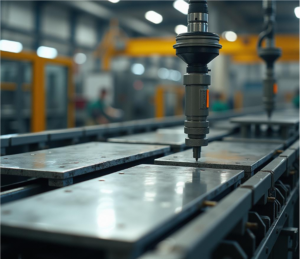
(1) Staged Pickling
Large-scale production often involves multiple pickling stages to target different oxide types and impurities:
Initial Pickling
- Purpose: Remove most oxide layers and loose contaminants.
- Acid: Lower-concentration nitric or mixed acids. Temperature: 25–40°C. Time: 5–15 minutes.
- Note: Focuses on easily removable oxides to prevent excessive or uneven corrosion in the main pickling stage.
Main Pickling
- Purpose: Deep removal of tough oxide layers and uniform surface roughness adjustment.
- Acid: Higher-concentration mixed acids (e.g., Nitric Acid 10%–15% + Hydrofluoric Acid 1%–3%). Temperature: 40–60°C. Time: 5–20 minutes, depending on oxide thickness.
- Note: Monitor the reaction closely to prevent overcorrosion. Use visual inspections or surface testing methods as needed.
(2) Soaking and Surface Stabilization
After pickling, a soaking phase is often necessary:
- Purpose: Balance acid absorption on the titanium surface, prevent localized corrosion, and ensure uniform micro-level surface conditions.
- Solution: Same acid formula as pickling but with reduced concentration or temperature (e.g., room temperature–30°C).
- Time: 3–10 minutes, adjusted based on surface observations and requirements.
- Monitoring: Inspect surface cleanliness and color changes periodically; gentle stirring may be used to ensure even soaking.
4. Post-Treatment Cleaning and Drying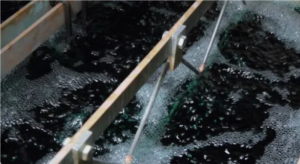
Multi-Stage Washing
- Immediately rinse with running water or in multiple wash baths to remove residual acids.
- Typically involves 2–3 stages, each lasting 1–3 minutes. For high-purity requirements, the final rinse may use deionized water to avoid ionic contamination.
Neutralization (Optional)
- For sensitive applications, immerse the material briefly in a weak alkaline solution (e.g., dilute ammonia or sodium carbonate) to neutralize remaining acids.
- Time: 2–5 minutes. Concentration and temperature should be controlled to avoid other forms of corrosion or deposits.
Drying and Inspection
- Use hot air or natural drying to ensure the surface is free from watermarks and residues.
- For high-standard products, drying in a cleanroom may be required to prevent recontamination.
- After drying, perform a visual inspection. If discoloration or residual oxides remain, consider reprocessing or touch-ups.
5. Process Monitoring and Record-Keeping
- Acid Concentration and Temperature Monitoring: Use online sensors or regular sampling to track acidity, temperature, and metal ion levels, ensuring consistency.
- Equipment and Environment Monitoring: Regularly inspect acid tanks, temperature controls, and ventilation systems to prevent accidents like temperature spikes or acid leaks.
- Process Data Logs: Maintain detailed records of production parameters to optimize processes and troubleshoot issues efficiently.
Summary
The parameters and workflow for pickling and soaking are critical for ensuring titanium’s surface quality and enhancing its performance in later stages.
- Accurate acid preparation, pre-treatment, staged pickling, controlled soaking, and thorough washing and drying effectively remove oxides, stains, and impurities.
- Proper control of key parameters like acidity, temperature, and soak time minimizes base material corrosion and defects.
- Process monitoring and record-keeping ensure batch consistency, laying a solid foundation for applications like welding, coating, plating, and electrochemical processes.
Cost and Timeline for Pickling and Soaking Titanium Materials
In titanium processing, pickling and soaking are essential steps to ensure surface quality and improve performance for subsequent applications. With our extensive experience in titanium surface treatment, we are pleased to share key factors influencing costs and timelines, along with practical advice to help you optimize your projects.
1. Key Factors Affecting Costs and Timelines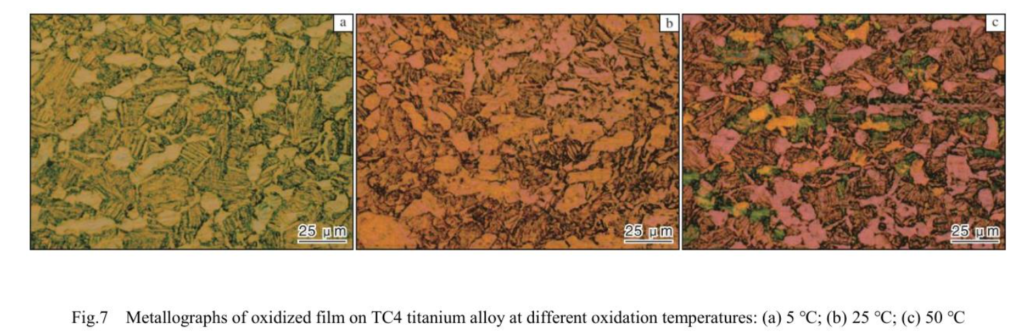
Oxide Thickness and Surface Condition
- For titanium with thick oxide layers or burn marks caused by high temperatures or prolonged use, we use stronger acids and longer soaking times, which increase material and labor costs.
Process Complexity
- For light oxidation, we offer single or dual-stage pickling processes, which are quicker and more cost-effective. However, materials requiring multi-stage pickling, precise temperature control, or pre-treatment such as blasting will result in higher costs and longer timelines.
Batch Size and Production Planning
- For large batches, we optimize production schedules and consolidate orders, which helps reduce per-unit costs and delivery times while maintaining high-quality standards.
Environmental and Safety Compliance
- We strictly follow environmental regulations and safety standards when handling acid waste and fumes. Projects requiring advanced environmental or safety measures may incur additional costs and longer lead times.
2. Cost and Timeline Estimates
The table below outlines typical costs and timelines for light, moderate, and heavy oxidation levels. These are general references; actual prices and durations depend on factors like material specifications, batch size, and environmental requirements.
Oxidation Level | Typical Condition | Recommended Process | Cost Range (RMB/kg) | Timeline (Workdays) | Notes |
---|---|---|---|---|---|
Light | Minor oxidation, oil stains, or surface debris | Single/double-stage pickling + short soaking, normal temp | 5–10 | 3–5 | Simple process, ideal for bulk orders of lightly oxidized titanium with basic surface requirements. |
Moderate | Visible oxidation from heat or welding | Multi-stage pickling + activation soak at 40–50°C | 10–15 | 5–7 | Suitable for most industrial-grade titanium, balancing efficiency and quality while protecting the base material. |
Heavy | Thick oxide layers, welding residue, or burn marks | Strengthened multi-stage pickling + blasting pre-treatment + longer soaking at 50–60°C | 15–25 | 7–10 | Designed for high-quality requirements or heavily oxidized materials; involves more complex processes. |
Note: The above estimates are for reference only. Actual costs and timelines may vary based on material conditions, specifications, and your specific surface quality requirements.
3. Tips to Control Costs and Timelines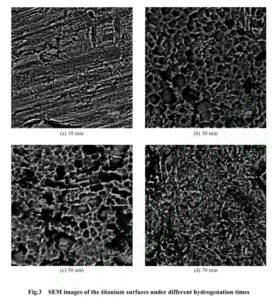
Pre-Treatment
- To reduce the difficulty of pickling, we recommend pre-cleaning steps like degreasing, light sanding, or blasting. These steps help shorten processing time and minimize acid usage.
Batch Planning
- If you have multiple shipments or ongoing requirements, consolidating them into a single production cycle can save costs by reducing setup time and equipment adjustments.
Real-Time Monitoring and Adjustments
- We monitor pH levels, temperatures, and metal ion concentrations during pickling to adjust soaking times and parameters as needed, ensuring stable quality and minimizing rework.
Environmental Compliance
- Our waste acid treatment and fume collection systems meet strict environmental standards, reducing environmental impact and avoiding delays or extra costs due to compliance issues.
Summary
The cost and timeline for pickling and soaking depend on the material’s oxidation level, batch size, process complexity, and environmental and safety requirements.
- For light oxidation, we offer faster and more affordable solutions suitable for basic applications.
- For moderate or heavy oxidation, multi-stage processes with close monitoring ensure high-quality results, albeit with higher costs and longer timelines.
If you have specific requirements or questions about pricing and delivery, feel free to contact us. We will provide tailored solutions based on your project needs, ensuring excellent surface quality and efficient production for your titanium materials.
Common Issues and Solutions in Pickling and Soaking
During the pickling and soaking of titanium and other metals, some common process and quality issues may arise. Based on our years of practical experience, we have summarized the following frequent issues and their solutions to help you plan and manage your projects more effectively.
1. Uneven Pickling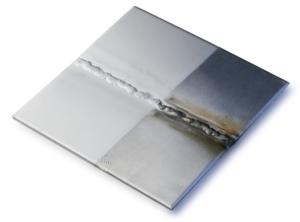
Symptoms
- Oxide layers are not completely removed, leaving patches or discoloration.
- Inconsistent adhesion or bonding strength in subsequent coating, plating, or welding processes, affecting final performance.
Causes
- Uneven acid distribution: Poor acid circulation during soaking leads to insufficient reaction in some areas.
- Overcrowded workpieces: Overloading or improper placement creates dead zones, preventing acid contact.
- Temperature or concentration gradient: Inconsistent temperature or acid concentration in the tank affects the pickling process.
Solutions
- Improve acid circulation: Use mechanical stirring or pumps to ensure uniform acid flow and eliminate stagnant zones.
- Optimize workpiece arrangement: Arrange items in layers or process in smaller batches to allow full acid contact.
- Enhance temperature and concentration control: Use multi-point sensors and monitoring systems to maintain uniform tank conditions.
2. Over-Corrosion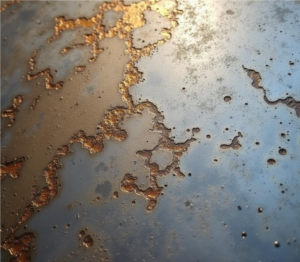
Symptoms
- Visible pitting, pinholes, or extensive base material damage, reducing mechanical strength or corrosion resistance.
- Surface appears dark, brittle, or with residual white spots.
Causes
- Excessive acid concentration or prolonged soaking time beyond recommended limits.
- Uncontrolled temperature: High temperatures accelerate acid erosion.
- Surface impurities: Residues like salts or alkalis react with acid, causing localized “hot spots.”
Solutions
- Precisely control acid concentration and time: Conduct pre-tests to determine optimal acid formulation and soaking duration.
- Temperature regulation: Use stable heating systems with monitoring and alarms to keep temperature within permissible ranges.
- Pre-treatment: Remove oils, alkalis, or residues before pickling to enhance consistency.
3. Acid Residue or Surface Contamination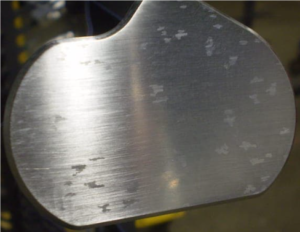
Symptoms
- Residual acid or corrosion by-products remain after pickling, appearing as spots or powdery deposits.
- Reduced coating or plating adhesion; surface corrodes again during storage or transport.
Causes
- Incomplete washing: Insufficient rinsing steps leave acid residues.
- Improper drying: Moisture and acid get trapped in corners or gaps during drying.
- Contaminated environment: Dust or chemical gases in the workspace cause secondary contamination.
Solutions
- Thorough multi-stage washing: Implement 2–3 washing steps, using deionized water in the final stage for maximum cleanliness.
- Efficient drying: Use hot air or vacuum drying to minimize moisture retention; seal components promptly if needed.
- Improve workspace environment: Ensure clean, ventilated areas for washing and drying to avoid recontamination.
4. Hydrogen Embrittlement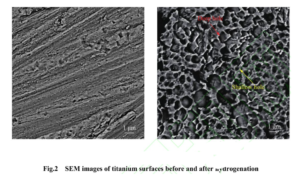
Symptoms
- Metals like titanium or zirconium become brittle, with reduced ductility and toughness.
- Microcracks or fractures appear during subsequent mechanical or thermal processes.
Causes
- High hydrogen ion concentration: Excessive hydrofluoric acid or hydrogen ions in the pickling solution penetrate the metal lattice.
- Prolonged soaking time: Extended exposure increases hydrogen absorption.
- Lack of dehydrogenation treatment: Without post-pickling heat treatment, hydrogen embrittlement risk rises.
Solutions
- Optimize acid formulation: Reduce hydrofluoric acid concentration or add inhibitors to minimize hydrogen penetration.
- Shorten soaking time: Use shorter, repeated pickling cycles to reduce hydrogen absorption.
- Dehydrogenation treatment: Perform heat treatment (e.g., 400–650°C) after pickling to release absorbed hydrogen.
5. Surface Roughness Out of Spec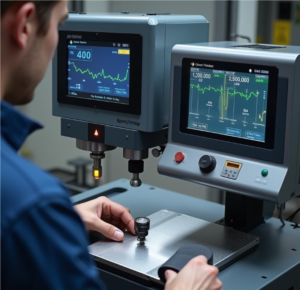
Symptoms
- Surface roughness (Ra, Rz) does not meet specifications; uneven textures or over-etched areas affect appearance and functionality.
- Excessive roughness affects coating thickness uniformity, while insufficient roughness reduces adhesion strength.
Causes
- Aggressive pickling or extended operation time, causing uneven base metal dissolution.
- Uneven initial oxide layers: Varying oxide thickness leads to inconsistent etching.
- Inadequate pre-treatment: Residual welding slag or tough oxides cause over-etching in certain areas.
Solutions
- Segmented or targeted pickling: Use localized or phased pickling for areas with varying oxidation levels.
- Monitor pickling rate: Use online thickness measurement tools or surface checks to stop soaking at the right time.
- Pre-treatment adjustments: Mechanically treat heavily oxidized or welded areas to avoid uneven corrosion during pickling.
Summary
Issues in pickling and soaking often arise from acid formulation, soaking time, temperature control, and pre-treatment steps. Based on years of production experience, we recommend the following best practices to minimize risks and ensure stable, high-quality results:
- Thorough pre-treatment: Effective degreasing, blasting, and impurity removal reduce the likelihood of uneven pickling or over-etching.
- Accurate process monitoring: Use real-time tracking of acid concentration, temperature, and hydrogen content, adjusting immediately if deviations occur.
- Multi-stage washing and drying: Prevent acid residue and contamination with staged cleaning and prompt drying.
- Dehydrogenation for sensitive metals: Perform targeted heat treatments for hydrogen-prone materials to maintain mechanical properties.
We are committed to professional, precise, and reliable production practices, ensuring every detail is carefully managed. If you have questions or specific requirements, we welcome the opportunity to collaborate and provide tailored solutions for your unique needs.
Chapter 2:Pickling and Soaking of titanium anodes
Common Questions About Pickling Solutions for Titanium Anodes
In the production of titanium anodes, pickling and soaking are crucial steps to ensure surface quality and activation levels. We understand that as a purchaser, you may be concerned about the types of acids used, their concentrations, and temperature control. The following information will help you better understand and evaluate the pickling process.
1. What Acids Are Used for Pickling?
Different acids serve distinct purposes in removing oxide layers, activating surfaces, and meeting environmental and safety requirements. Common choices include:
Nitric Acid (HNO₃)
- Primary Role: Effectively removes oxide films and helps activate the surface.
- Features: Mature waste treatment processes, suitable for large-scale industrial use.
- Tip: High concentrations require enhanced safety measures; when mixed with hydrofluoric acid, precise ratio control is essential.
Hydrofluoric Acid (HF)
- Primary Role: Strong dissolving ability for stubborn oxide layers, quickly cleaning the surface.
- Features: Enhances surface roughness, providing an excellent foundation for precious metal coatings.
- Tip: Highly corrosive and hazardous; strict operational and protective measures are required, as well as higher waste treatment costs.
Hydrochloric Acid (HCl) or Sulfuric Acid (H₂SO₄)
- Primary Role: Auxiliary acids to reduce costs or enhance cleaning efficiency when combined with other acids.
- Features: Widely available and relatively affordable; requires good ventilation and acid mist control.
- Tip: Ensure robust workshop safety measures to minimize gas pollution during use.
Mixed Acids (e.g., Nitric Acid + Hydrofluoric Acid + Additives)
- Primary Role: Balanced formulas that combine efficient oxide removal with base material protection, suitable for various requirements.
- Features: Flexible component ratios tailored to material thickness or surface quality needs.
- Tip: Precise mixing and careful operation are required to avoid localized corrosion or excessive acid mist.
Why Does the Type of Acid Matter?
Different acids vary in their removal speed, activation effects, and environmental treatment challenges. Based on your titanium anode’s oxide thickness, coating requirements, and project budget, we recommend the most suitable acid or acid mixture.
2. What Are the Typical Concentrations of Pickling Solutions?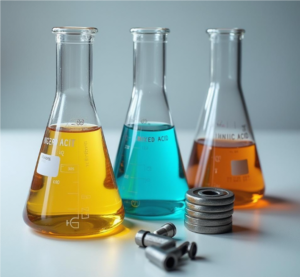
Acid concentration directly affects oxide removal efficiency, surface roughness, and corrosion depth. We typically control concentrations within the following ranges:
Low Concentration (e.g., HF 0.5–2%, HNO₃ 5–10%)
- Best For: Light oxidation or basic surface activation.
- Advantages: Minimal material loss, precise control of surface morphology; ideal for small batches or high-value products.
- Tip: Removal speed is slower, so production cycles may be longer, requiring proper time planning.
Medium Concentration (e.g., HF 2–5%, HNO₃ 10–15%)
- Best For: Moderate oxidation requiring fast oxide removal while protecting the base material.
- Advantages: Efficiently removes stubborn oxide layers within a reasonable timeframe; suitable for most industrial-grade titanium anodes.
- Tip: Use online monitoring (temperature, pH) to prevent over-corrosion or hydrogen embrittlement.
High Concentration (e.g., HF >5%, HNO₃ >15%)
- Best For: Thick or extensive oxidation layers needing rapid cleaning; also used for heavily contaminated materials.
- Advantages: Shortens batch processing times and increases production capacity.
- Tip: Higher risk of corrosion; precise control of acid concentration and soaking duration is necessary. Safety and waste treatment costs also rise.
Why Does Concentration Matter?
Higher concentrations work faster but can cause more damage to the base material. We determine the optimal concentration range based on your titanium anode’s condition and our experience, ensuring efficiency and quality while minimizing unnecessary corrosion.
3. What Temperature Range Is Used for Pickling?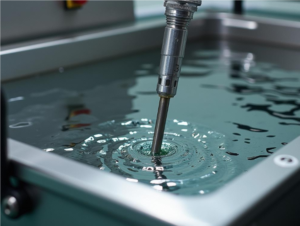
Temperature significantly impacts the pickling rate, surface uniformity, and process stability. We typically operate within these temperature ranges:
Low-Temperature Pickling (Room Temperature–30°C)
- Features: Slower chemical reactions allow precise control of surface roughness, ideal for high-quality products.
- Tip: Longer processing times may require careful capacity and delivery planning.
Medium-Temperature Pickling (40–50°C)
- Features: Balances production efficiency and surface uniformity, making it the most common range for moderately oxidized titanium anodes.
- Tip: Ensure stable temperature systems and proper stirring to avoid localized overheating.
High-Temperature Pickling (60–70°C or Higher)
- Features: Greatly accelerates pickling for stubborn or heavy oxide layers.
- Tip: Increased corrosion risks require precise monitoring. Waste and acid mist treatment costs are also higher.
Why Does Temperature Matter?
Improper temperatures can lead to over-corrosion, uneven pickling, or roughness issues. Our pickling tanks are equipped with multi-point temperature sensors and circulation systems to maintain uniformity. For high-temperature processes, we also implement enhanced ventilation and exhaust treatments to ensure safety and compliance.
Summary
In titanium anode pickling and soaking, acid type, solution concentration, and temperature control are the three fundamental factors. Together, they determine:
- Oxide layer removal speed and thoroughness
- Surface activation effects and microscopic structure
- Corrosion risk and coating adhesion
- Overall process costs and environmental impact
We evaluate the material specifications, oxidation levels, production volume, and your performance needs to recommend the best solutions. During production, our online monitoring and expert technical team dynamically adjust acid formulas, operating temperatures, and soaking times to achieve optimal results.
If you have further questions about processes or costs, please feel free to reach out. We’re committed to providing customized, efficient, and reliable pickling and soaking services to meet your specific needs.
Why Does Pickling and Soaking Affect the Lifespan of Titanium Anodes?
1. How Does Pickling and Soaking Ensure a Clean Surface?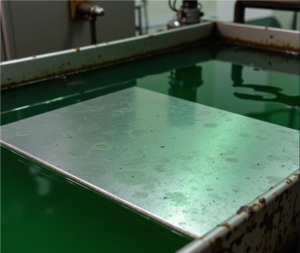
During the production of titanium anodes, any remaining oxide layers, impurities, or microcracks on the base material can accelerate failure during use.
- Key Benefits of Pickling and Soaking:
- Removes stubborn oxide layers and contaminants.
- Adjusts surface roughness to enhance bonding with precious metal or oxide coatings.
- Reduces microcracks and pores, minimizing localized corrosion risks.
A thorough pickling process results in a cleaner surface, improving coating adhesion and uniformity.
2. What Process Parameters Impact Titanium Anode Quality?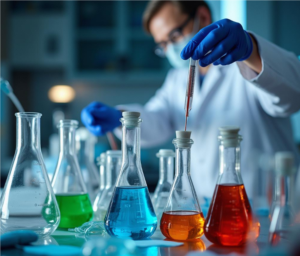
While the type of acid, concentration, and temperature are all important, the following factors are especially critical:
Pickling Time
- Too short: Incomplete oxide removal.
- Too long: Risk of over-corrosion or hydrogen embrittlement.
Acid Concentration
- Too low: Ineffective removal of tough oxide layers.
- Too high: Surface roughness becomes uncontrollable, and base material is damaged.
Soaking Temperature
- Too low: Slower pickling efficiency, affecting productivity.
- Too high: Accelerates corrosion, increasing safety and environmental risks.
Midway Checks and Washing
- Without periodic checks or multi-stage washing, residual acid or contamination can reattach to the surface.
3. Is There Data to Show How Pickling Affects Lifespan?
The table below shows example data illustrating how pickling parameters influence the lifespan and performance of titanium anodes (for reference only, as actual values depend on materials, coatings, and conditions).
Pickling Conditions | Surface Roughness (Ra, μm) | Coating Adhesion (1–5) | Accelerated Lifespan (hours) (in a common electrolytic environment) |
---|---|---|---|
Low Concentration + Low Temperature + Short Time (HF 1.0%, HNO₃ 8%, 25°C, 5 min) | 0.3 | 3 | 3000 |
Medium Concentration + Medium Temperature + Optimal Time (HF 2.5%, HNO₃ 12%, 45°C, 10 min) | 0.5 | 4 | 4500 |
Medium Concentration + Medium Temperature + Multi-Stage (HF 2.5%, HNO₃ 12%, 45°C, 2×5 min) | 0.4 | 5 | 5000+ |
High Concentration + High Temperature + Long Time (HF 5.0%, HNO₃ 15%, 60°C, 15 min) | 0.8 | 3 | 3500 |
Key Indicators:
- Surface Roughness (Ra): Moderate roughness helps coatings bond better, but excessive roughness can cause corrosion or peeling.
- Coating Adhesion (1–5): Higher numbers indicate better adhesion, tested through methods like grid or peel testing.
- Accelerated Lifespan (hours): Simulated service time under specific electrolytic conditions, with higher numbers indicating better durability.
From the data, a medium concentration, medium temperature, and multi-stage pickling process balances efficiency, surface quality, and base material protection, extending anode lifespan.
4. How Can Optimizing Pickling Extend Titanium Anode Lifespan?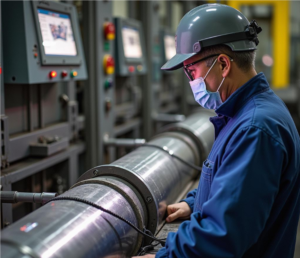
Multi-Stage Pickling
- Ensures even oxide removal and allows for real-time surface checks, reducing over-corrosion risks.
Real-Time Monitoring and Washing
- Monitor acid concentration, pH, and temperature to make timely adjustments; washing removes detached oxides, preventing reattachment.
Post-Treatment Drying and Clean Storage
- After pickling, quickly rinse and dry the material to prevent residual acid or moisture. Store in a clean environment to avoid contamination before coating.
5. What Are the Benefits for Purchasers?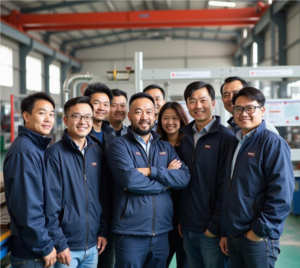
- Improved Production Stability: Longer-lasting anodes reduce failure rates and downtime, saving maintenance and replacement costs.
- Lower Environmental and Safety Pressure: Optimized pickling reduces acid use and waste treatment costs.
- Enhanced Product Competitiveness: Reliable, durable titanium anodes strengthen your reputation and market position in downstream industries like electrolysis and plating.
Summary
Why does pickling and soaking affect titanium anode lifespan? Because it significantly impacts surface cleanliness, activation, and coating adhesion.
- By using optimal process parameters (such as concentration, temperature, and timing), oxide layers are effectively removed while minimizing material loss and over-corrosion.
- Proper surface roughness and uniformity enhance the bonding of precious metal or functional coatings, extending the overall lifespan of the anodes.
If you have specific needs or want to learn more about customized parameters, feel free to contact us. We are dedicated to providing high-performance, long-lasting titanium anode solutions tailored to your production requirements.
Why Are Post-Treatment and Drying Just as Important as Pickling and Soaking?
In the production of titanium anodes, the steps after pickling and soaking are crucial to ensuring the surface is ready for coating, welding, or electrochemical applications. Drawing from extensive experience, we share the key points and optimization strategies for post-treatment and drying to achieve the best results.
1. Multi-Stage Washing: How Do We Ensure a Truly Clean Surface?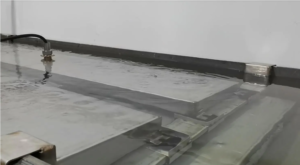
Multiple Washing Steps
- Purpose: To thoroughly remove any residual acid or impurities from the surface and crevices, preventing further corrosion or contamination.
- Process: We typically perform 2–3 washing stages using running water or circulating water. For the final wash, we may switch to deionized or purified water to minimize residual ions.
Water Temperature and Duration
- Temperature: When materials leave the pickling tank at high temperatures, sudden cooling can cause thermal stress. We match the water temperature to the material for a smooth transition.
- Duration: Washing time varies between 1–5 minutes, depending on acid concentration and the complexity of the material’s surface. For intricate areas, extended washing may be necessary.
Online Monitoring and pH Checks
- Real-Time Monitoring: We regularly test the pH or conductivity of the washing water to ensure thorough cleaning. If residual acid or metal ion levels are high, additional washing or water replacement is carried out.
Benefits:
- Ensures the surface is clean and neutral, ready for the next process.
- Minimizes contamination risks during subsequent coating or electroplating, improving adhesion.
2. Neutralization and Passivation: Are They Necessary?
Neutralization with Weak Alkali Solutions
- How It Works: For some applications, we immerse titanium briefly in a weak alkali solution (e.g., diluted ammonia or sodium carbonate) to neutralize residual acid.
- When to Use: This step is critical if any remaining acid could interfere with subsequent processes, such as catalyst coating or electrochemical testing.
Surface Passivation or Pre-Treatment
- Purpose: Depending on the requirements, we may apply a light passivation or pre-treatment to prepare the surface for high-temperature coatings or specialized electrochemical environments.
- Tip: Not all titanium anodes require this step. Its necessity depends on compatibility with the next process and coating type.
Benefits:
- Stabilizes the chemical state of the surface, especially for sensitive coatings or environments.
- Reduces the risk of hidden damage caused by residual acidic ions.
3. Drying Methods and Environmental Control: Why Do They Matter?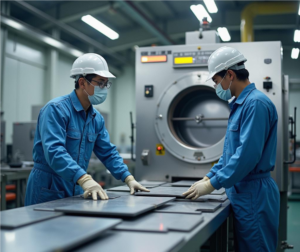
Hot-Air Drying vs. Natural Drying
- Hot-Air Drying: Speeds up water evaporation, reducing exposure time to external contaminants and preventing oxidation. Ideal for orders requiring immediate processing, such as coating or welding.
- Natural Drying: More energy-efficient but requires a clean, dry environment. For high-spec applications, it’s critical to avoid dust or moisture affecting the surface.
Cleanroom or Controlled Environment
- For titanium anodes with extremely high surface quality requirements, such as precision electrodes or medical applications, we recommend final drying in a cleanroom or a controlled environment.
- This prevents fine particles or oils from contaminating the surface, ensuring optimal cleanliness.
Surface Inspection and Touch-Ups
- After drying, we conduct visual inspections or basic tests (e.g., optical scans or microscopic checks). Any residual oxide films, spots, or uneven areas are addressed immediately with touch-ups or re-pickling.
Benefits:
- Reduces risks of surface defects caused by improper drying.
- Establishes a strong foundation for subsequent coating or assembly steps.
4. Storage and Transportation: How Do We Protect the Surface?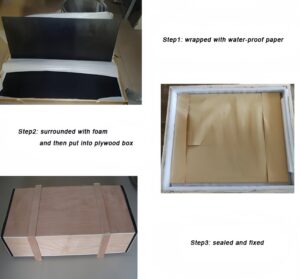
Protective Packaging
- After drying, we use moisture-proof and dust-proof materials (e.g., vacuum packaging, bubble wrap, or barrier paper) to safeguard the anodes during transportation.
Timely Transition to the Next Process
- For orders requiring subsequent coating or surface treatment, we recommend coordinating schedules to minimize time between drying and processing, avoiding re-oxidation.
Environmental Conditions
- Storage and transportation environments—humidity, temperature, and dust levels—can affect the surface. We provide tailored storage solutions based on storage duration and regional climate.
Benefits:
- Preserves the cleaned and prepared surface.
- Reduces additional costs and risks associated with re-cleaning or re-pickling.
Summary
Post-treatment and drying are just as critical as the pickling process itself. We believe that only by executing thorough cleaning, neutralization, drying, and protective packaging can your titanium anodes achieve optimal performance and reliability in use.
- Multi-stage washing removes residual acids and impurities completely.
- Neutralization and passivation are vital for sensitive or high-demand applications.
- Drying and clean environments ensure final surface cleanliness, directly impacting coating and installation quality.
- Professional packaging and storage prevent damage or contamination during transportation or downtime.
If you have any questions about post-treatment steps or specific requirements, please reach out. With years of expertise and technical advantages, we are committed to providing detailed solutions that ensure your titanium anodes are delivered with consistent and reliable quality from production to application.
Chapter 3:Support and Optimization
How Do We Ensure the Stability and Quality of the Pickling Process?
In titanium anode production, pickling is a critical step. Without stable and repeatable process controls, product quality can vary between batches, affecting the anode’s performance. Here’s how we monitor and control the process to deliver consistent and reliable titanium anode products.
1. How Do We Monitor and Test the Pickling Quality?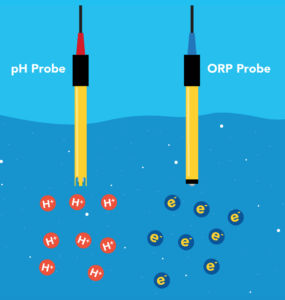
pH and Acid Concentration Monitoring
- Online or Spot Testing: We use pH sensors in key areas of the pickling tank or perform regular sampling to measure pH and acid concentration.
- Adjustments: If pH or acid levels deviate from the set range (e.g., ±0.2 pH), we immediately add acid or replace part of the solution to maintain stability.
Oxidation-Reduction Potential (ORP)
- Why ORP Matters: ORP measures the solution’s oxidation strength, helping us evaluate the efficiency of oxide removal.
- When We Use It: ORP data, combined with material thickness and composition, helps optimize soaking time and stirring intensity.
Surface Quality Checks
- Visual or Optical Inspection: During pickling, we randomly check the surface for discoloration, uniformity, or issues like over-corrosion or spots.
- Non-Destructive Testing: For critical batches, we use laser or optical tools to verify complete oxide removal.
Pickling Solution Maintenance
- Regular Replacement: We schedule partial or full solution changes based on production volume and test results to maintain activity and avoid contamination.
- Waste Treatment: Our robust waste management system ensures safe disposal and compliance with environmental standards.
Summary:
With continuous monitoring of pH, ORP, and surface conditions, we detect and correct potential issues immediately to ensure consistent quality.
2. How Do We Test the Surface Quality and Activity of Titanium Anodes After Pickling?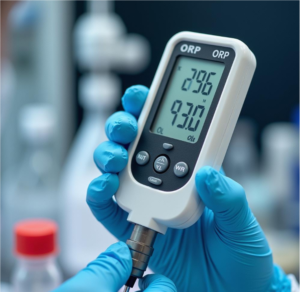
Surface Inspection and Roughness Testing
- Visual Inspection: After pickling, we evaluate surfaces under clean and dry conditions for uniformity, oxide residue, or spots.
- Roughness Testing: For anodes requiring specific microstructures, we use roughness testers (e.g., Ra and Rz values) to verify that the surface meets standards.
Electrochemical Testing
- Open Circuit Potential (OCP): We test anodes in simulated electrolytic solutions to assess surface activation.
- Polarization Curve Testing: For detailed evaluations of corrosion resistance and catalytic performance, we conduct polarization tests or Electrochemical Impedance Spectroscopy (EIS).
Microscopic and Metallurgical Analysis (Optional)
- Microstructure Checks: For high-end or critical applications, we use microscopes or Scanning Electron Microscopy (SEM) to detect microcracks or pores.
- Coating Bonding Tests: For coated anodes, we test the adhesion between the base material and coating to prevent potential delamination.
Summary:
These tests allow us to quantify surface cleanliness and activation while predicting the anode’s performance in its working environment, providing assurance to our customers.
3. What Are Our Pickling Pass Rates, Defect Rates, and Rework Rates?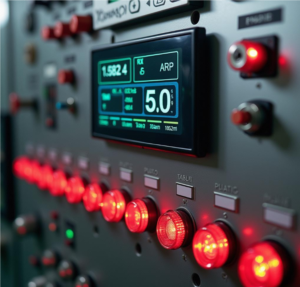
Definitions
- Pass Rate: The percentage of anodes that pass all inspections after pickling and proceed to the next process without issues.
- Defect Rate: The percentage of anodes with severe issues (e.g., over-corrosion or oxide residue) that cannot be repaired.
- Rework Rate: The percentage of anodes requiring additional processing (e.g., re-pickling) to meet standards.
How We Achieve High Pass Rates
- Comprehensive Process Database: We leverage extensive data on acid types, concentrations, temperatures, and material specifications to optimize the process.
- Real-Time Monitoring and Alerts: Deviations in key metrics like pH or ORP are addressed immediately to prevent batch-wide defects.
- Strict SOPs: From staff training to equipment maintenance, we follow detailed standard operating procedures to ensure consistency.
Transparent Data Sharing
- We provide batch pass rate reports and defect/rework records upon request, offering full transparency for evaluation.
- If an issue arises in any batch, we quickly analyze the cause and propose corrective actions to minimize impacts on delivery and costs.
Summary:
A high pass rate reflects our well-established and repeatable process, while low defect and rework rates demonstrate our commitment to consistent quality.
Conclusion
To ensure the stability and quality of the pickling process, we have implemented a robust system of monitoring and testing:
- Real-time process control (pH, ORP, surface checks) ensures quick detection and correction of potential issues.
- Comprehensive testing (visual inspection, roughness testing, electrochemical analysis) objectively verifies surface activation and reliability.
- Low defect and rework rates guarantee consistent results, helping you achieve stable supply and cost control.
If you have questions about our pass rates, defect rates, or testing methods, feel free to contact us. We are happy to provide tailored quality control strategies and technical support to meet your project’s specific needs.
Can We Customize Pickling Solutions for Specific Electrolytes or Operating Conditions?
In real-world applications of titanium anodes, different electrolytes (e.g., acidic, alkaline, chloride-rich, or high-salt environments) and specific conditions (e.g., high current density, long-term continuous operation) require unique surface properties. Using a standard pickling process may not provide the reliability and lifespan needed in these scenarios. That’s why we’ve developed a customized pickling approach to help you adapt to various applications.
1. Why Customize the Pickling Process?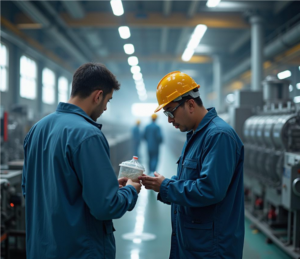
To Handle Diverse Electrolytes
- In chloride-rich electrolytes, for example, any surface microcracks or residual oxide layers can lead to localized corrosion or coating delamination after operation.
- By adjusting acid concentration, type, and soaking time, we can achieve optimal surface roughness and activation, enhancing the anode’s corrosion resistance and stability.
To Match Special Operating Conditions
- For anodes exposed to high current densities or high-temperature, high-pressure environments, we must prevent issues like over-corrosion or hydrogen embrittlement during pickling.
- Customized pickling allows precise adjustments to acid mixtures (e.g., hydrofluoric or nitric acids), balancing oxide removal with substrate protection.
To Improve Coating Adhesion
- Different coatings (precious metals or metal oxides) have specific requirements for surface roughness and energy. Custom pickling ensures the surface is ideal for coating adhesion and optimal electrochemical performance.
2. How Do We Create a Customized Pickling Solution?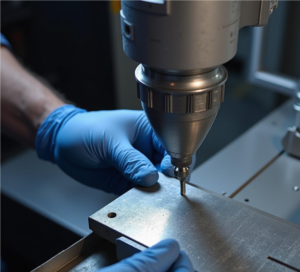
Understanding Your Application
- We start by discussing the electrolyte’s pH, temperature, ionic composition, and the anode’s operating conditions (e.g., current density, runtime).
- For example, in high-salt environments, we focus on eliminating potential corrosion sources like microcracks or inclusions.
Evaluating Surface Conditions and Targets
- If the substrate already has oxide layers or contaminants, we may recommend pre-treatment (e.g., blasting or alkaline washing) before matching the pickling formula.
- We set specific performance metrics, such as post-pickling roughness (Ra) or surface uniformity, based on your coating and application needs.
Trial Runs and Validation
- Before mass production, we conduct small-scale trials, monitor key parameters (e.g., pH, ORP, temperature), and test the product’s surface or accelerated aging.
- If results deviate from targets, we fine-tune acid ratios, temperature, or time for further optimization.
3. What Are the Practical Benefits of Customized Pickling?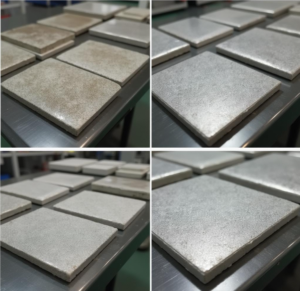
Extended Anode Lifespan
- Targeted removal of tough oxide layers and contaminants, while protecting the substrate, significantly reduces surface defects and lowers maintenance and replacement costs.
Enhanced Electrochemical Performance
- By optimizing surface roughness and activation, coatings perform better with improved catalytic efficiency and current distribution, increasing energy output or production rates.
Reduced Hidden Production Losses
- Preventing issues like coating delamination, rework, or unexpected downtime saves additional costs and ensures consistent production stability.
4. Case Study: Customized Pickling for Chloride-Rich Environments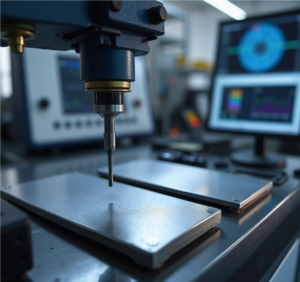
- Background: A client’s process involved high-chloride electrolytes and elevated temperatures. Standard pickling resulted in localized corrosion and coating delamination.
- Solution:
- Adjusted the hydrofluoric and nitric acid ratios in the pickling solution.
- Implemented a two-stage pickling process (pre-cleaning and main pickling) with lower soaking temperatures and real-time monitoring.
- Added a light passivation step post-pickling to suppress hydrogen absorption.
- Results:
- The new process delivered smoother, more uniform surfaces with fewer microcracks.
- Coating adhesion improved, extending anode lifespan by 20–30% and reducing overall maintenance costs.
5. How to Work With Us on a Customized Pickling Solution?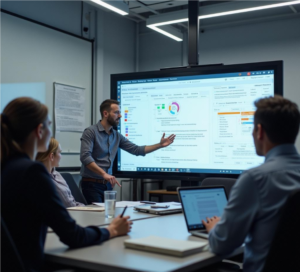
Requirement Discussion
- Share the basic operating conditions, anode specifications, and performance goals. We’ll use our database and past experience to propose an initial solution.
Trial Production and Feedback
- Before scaling up, we can conduct small-scale trials to quickly validate the solution’s feasibility. Accelerated lifespan tests or electrochemical analyses can also be performed.
Mass Production and Continuous Optimization
- During production, we strictly follow SOPs and monitoring protocols, continuously collecting process data to support future scaling or product iterations.
Note:
If your project involves unique electrolyte compositions, operating temperatures, or usage patterns, please communicate these details early. This ensures we can customize the pickling process to maximize your titanium anode’s quality and lifespan.
Summary
Customized pickling goes beyond simple adjustments to acid concentration. It integrates information about the electrolyte environment, substrate condition, and coating requirements, verified through testing, to ensure your titanium anodes perform optimally in specific conditions.
- Through detailed discussions, we tailor pickling parameters, pre-treatment processes, and even post-pickling steps to meet your application needs.
- We focus on surface quality, cost control, and delivery timelines, helping you stand out in a competitive market.
If you have specific requirements or would like to explore solutions for complex applications, feel free to contact us. Our technical team is ready to provide professional, customized support to ensure your anodes deliver efficient and stable performance under any conditions.
How to Handle Periodic Cleaning and Maintenance of Titanium Anodes?
During prolonged use, titanium anode surfaces may accumulate inorganic deposits, residues, or experience localized performance degradation. If not addressed promptly, these issues can reduce anode efficiency and disrupt production. To help you maintain peak performance and extend anode lifespan while lowering operational costs, we offer a variety of periodic cleaning and maintenance solutions tailored to different applications and conditions.
1. What Periodic Cleaning Options Do We Offer?
The table below compares three common cleaning methods, their applicable scenarios, frequency, and cost structure, helping you select the right solution for your maintenance needs.
Cleaning Method | Applicable Scenarios | Frequency | Typical Cost | Notes |
---|---|---|---|---|
Light Cleaning (Weak Acid/Alkali) | 1. Minor surface deposits2. No significant drop in anode performance | Monthly or quarterly | Low cost(Included in routine maintenance) | Simple to perform and can be done on-site with minimal production disruption. |
Moderate Cleaning (Standard Pickling) | 1. Noticeable fouling or passivation2. Reduced capacity or current efficiency | Semi-annually or annually | Moderate cost(Pay-per-service or contract-based) | Requires off-site servicing or on-site assistance; ideal for removing stubborn deposits and restoring electrochemical performance. |
Deep Regeneration (Enhanced Pickling) | 1. Heavy carbon or multilayer deposits2. Surface aging or localized corrosion | Periodic (every 1–2 years) | Higher cost(Quoted separately) | Often combined with coating restoration or partial replacements; suitable for intensive repairs and performance recovery. |
How to Choose?
- For minor deposits without performance impact, light cleaning is sufficient to maintain activity.
- For visible fouling or reduced efficiency, moderate cleaning is recommended for timely recovery.
- For significant surface damage or corrosion, deep regeneration ensures thorough restoration.
2. How Are After-Sales Support and Maintenance Services Arranged?
Multi-Tiered Service Options
- Basic Technical Support: For light cleaning or simple maintenance, we provide guidance via phone, email, or remote consultation.
- On-Site or Off-Site Servicing: Moderate and deep cleaning typically require specialized equipment and pickling tanks. You can ship the anodes to our facility or request on-site service, depending on your production setup and location.
- Scheduled Inspections and Maintenance Contracts: For high-demand, large-scale operations, we offer annual or periodic maintenance contracts to pre-plan cleaning schedules and minimize downtime.
Costs and Billing
- Light Cleaning Support: Included in our complimentary after-sales services at no extra cost.
- Moderate and Deep Cleaning: Charged per service or bundled into maintenance contracts; pricing is determined based on operating conditions and anode specifications.
- Emergency or Expedited Services: For urgent capacity recovery, expedited off-site or on-site services are available, subject to an additional fee.
Key Tips:
- Regularly share anode performance data with us to detect early signs of degradation and intervene promptly, minimizing downtime and maintenance costs.
- For extreme operating conditions, consider adding preventive maintenance steps to extend anode lifespan and reduce risks.
3. How Do We Ensure Environmental Safety and Compliance During Maintenance?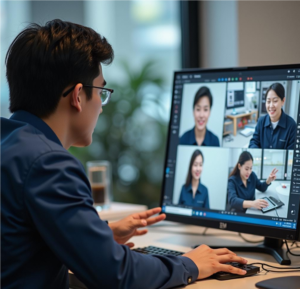
Professional Protection and Operations
- We strictly follow environmental safety protocols during all pickling and cleaning operations, using corrosion-resistant equipment and acid vapor collection systems to minimize impacts on personnel and the environment.
- Our technicians are specially trained to handle hazardous materials, preventing incidents like spills or splashes during the process.
Certifications and Compliance
- Certified under ISO 14001 (Environmental Management) and ISO 45001 (Occupational Health and Safety), we maintain robust procedures for waste liquid treatment, gas emissions, and worker safety.
- If your site has specific environmental or safety requirements (e.g., stricter waste discharge or air quality standards), we can create a customized plan to meet local regulations and industry norms.
Responsibility and Commitment
- We take full responsibility for environmental safety and compliance during cleaning or regeneration services, providing regular updates throughout the process.
- All equipment undergoes routine inspections, and operators are fully certified. For complex tasks, we conduct thorough risk assessments and safety setups before starting.
Why It Matters:
- Ensures maintenance operations do not cause additional disruptions or environmental harm to your production line or surroundings.
- Reduces the risk of incidents, giving you confidence in choosing our services while aligning with sustainability goals.
Summary
Periodic cleaning and maintenance of titanium anodes are critical to maintaining production efficiency and extending anode lifespan. Our light, moderate, and deep cleaning solutions, combined with flexible after-sales services, ensure professional support while keeping downtime and maintenance costs reasonable.
- Regular Maintenance: Prevent capacity loss and delay anode degradation.
- Comprehensive After-Sales Support: Remote consultation, on-site service, and off-site repair options to suit diverse needs.
- Environmental Compliance: Certified under ISO 14001 and ISO 45001, with multiple safeguards for safe and responsible operations.
If you have specific questions or plans regarding periodic cleaning or other maintenance needs, feel free to contact us. Our technical and customer service teams will provide tailored recommendations and quotes based on your production scale, capacity requirements, and location, ensuring your titanium anodes operate efficiently and reliably throughout their lifecycle.
Why Trust Us for Long-Term Titanium Anode Support?
In titanium anode production and application, focusing on just one step in the process is not enough. We understand that what customers truly need is end-to-end, sustainable technical support and professional service. From early consultation to quality control, ongoing maintenance, and future process development, we ensure the performance and lifespan of titanium anodes. Here’s why we are the partner you can rely on:
1. We Work Closely With You From the Start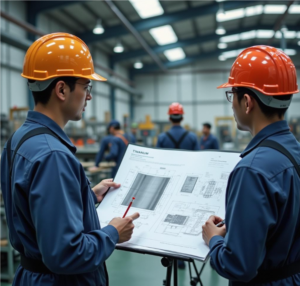
Understanding Your Needs
From the moment we receive your project requirements, we engage in one-on-one discussions to understand the operating environment, electrolyte properties, and production capacity needs. Based on this, we recommend the most suitable pickling process and post-treatment plan to build a strong foundation for your project.Tailored Solutions
Whether you have unique titanium substrate specifications or specific performance demands, our technical team customizes acid concentration, soaking temperature, and process steps to maximize surface cleanliness and substrate protection.
2. Comprehensive Quality Control and Reliable Delivery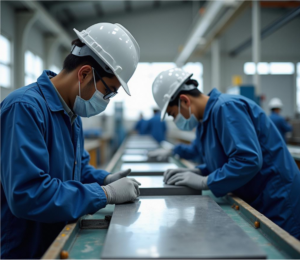
Strict Process Monitoring
During pickling and soaking, we maintain a comprehensive quality system with metrics such as pH, ORP, and surface activation. Real-time monitoring and multi-point testing ensure any fluctuation is quickly detected and corrected, avoiding batch-wide issues.Continuous Process Optimization
Leveraging extensive production experience and data, we analyze the pickling effectiveness and pass rates for every batch. If improvement opportunities are identified, we promptly optimize the process, ensuring your products maintain consistent top-tier quality.Thorough Inspection Before Shipping
Before delivery, all anodes undergo visual inspections, electrochemical testing, or other customized checks to ensure uniformity and durability when they reach your hands.
3. Post-Sales Maintenance and Long-Term Support
Periodic Cleaning and Maintenance
If your anodes experience fouling or performance degradation during use, we offer light, moderate, or deep cleaning solutions. We can arrange on-site servicing or factory maintenance to minimize downtime and maintenance costs.Flexible Service Options
Whether you have small-scale occasional needs or large-scale continuous applications, we can tailor maintenance contracts or technical support plans to help you manage production challenges effectively.Safety and Environmental Compliance
Certified under ISO14001 and ISO45001, we have robust systems for waste liquid treatment, safety protection, and operator training, ensuring compliance and peace of mind for your operations.
4. Research and Future Innovation: Partnering for Growth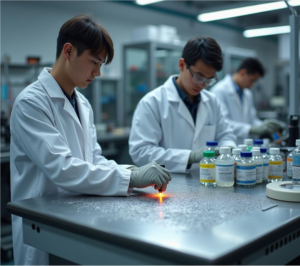
Ongoing R&D
As industries seek higher efficiency and lower energy consumption in electrochemical applications, we continuously improve pickling formulas, introduce advanced testing tools, and explore nanoscale surface treatments to push the boundaries of performance.Customer Feedback Drives Innovation
We value every piece of customer feedback—new conditions, materials, and challenges drive our process improvements and new product development, helping you stay ahead of market trends and competition.Building Long-Term Partnerships
Our long-term collaboration extends beyond custom product delivery. We provide support in process upgrades, production line transformations, and new field exploration, becoming a trusted partner for growth in titanium anode technology.
Conclusion
- We offer more than just titanium anode products or isolated pickling services. We provide an integrated solution, covering early consultation, tailored process development, rigorous quality control, ongoing maintenance, and continuous R&D.
- From project start to long-term maintenance, we are committed to professionalism, efficiency, and sustainability, positioning ourselves as your most reliable partner in the titanium anode industry.
- Whatever challenges or innovation needs you face, we are ready to collaborate. Let’s work together to explore the future of titanium anode processes and technology.
Chapter 4:Summarize
Ehisen wants you to know
At Ehisen, we understand that the key to producing high-quality titanium anodes begins with a meticulous surface pre-treatment process. Before the application of precious metal coatings like ruthenium-iridium or platinum, titanium substrates undergo a critical acid pickling and immersion procedure. This vital step ensures the surface is properly activated and free of impurities, setting the foundation for superior coating adhesion and long-lasting performance.
Our pre-treatment process involves carefully controlled acid washing and immersion, designed to thoroughly clean and activate the titanium surface. By effectively removing any contaminants and oxidation, we create the ideal surface for the subsequent precious metal coating. This ensures both the quality and longevity of the finished titanium anodes, helping you achieve optimal performance in your electroplating, cathodic protection, and water treatment applications.
With Ehisen’s expertise in titanium anode production, we ensure that each anode meets the highest standards of quality and reliability. We prioritize precision in every step, including this crucial pre-treatment phase, to ensure that your anodes perform consistently and efficiently across their entire lifecycle.
Let us collaborate with you to deliver precision-engineered titanium anodes that not only meet but exceed your specifications, providing long-term value and reliable performance.
Supply & services
Our value go beyond titanium processing
Finding a reliable processor of titanium products is essential to your business success, and Ehisen is here to be that partner.